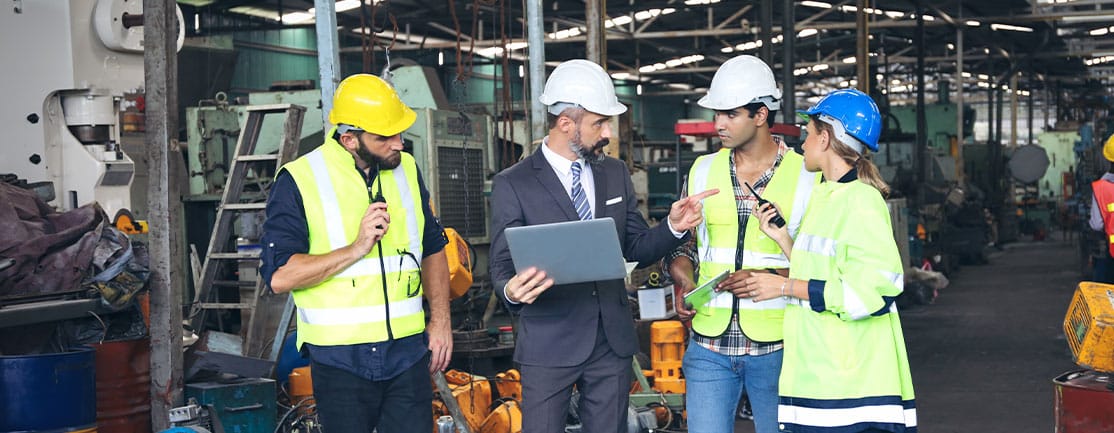
How to make process improvement part of your factory’s digital DNA
The workplaces of today are complex, global networks of transactional enterprises fueled by digital disruption. It creates new business models, changes value streams, and incites change faster than ever before. When the global pandemic entered the fray in 2020, matters became even more frenetic. All this demands a technology-enabled approach to continuous process improvement.
The next generation of process improvement programs presents a challenge to design and implement them sustainably in the new economy with the right approach, focus, velocity, agility and simplicity. This needs to be executed while eliminating or working within the organization’s realistic constraints and dynamic operating models.
It means following a blended strategy comprising Deming’s well-established PDCA model, innovation, the integration of enabling technology, and flexible improvement across diverse operating environments. While also a well-integrated system of improvement similar to the Toyota Production System (TPS), it’s a more dynamic system that leverages technology and picks improvement opportunities on a broader scale.
As corporate production systems evolve into next-generation “digital operating systems” (DOS), organizations will need to maintain a foundation of continuous improvement to drive their digital transformation ambitions. This new framework’s three key elements are a more innovative and integrated approach to improvement, a different focus via the fusion of improvement and enabling technology, and the development of a new organizational core competency of “improving how we improve.”
Download the white paper Digital operating systems: The next -generation of corporate production systems for the building blocks of a successful transition to DOS.

Why the need for business process improvement?
Transformative technologies proliferated in the workplace even before the pandemic, enabling organizations to innovate and thrive in an increasingly digital world. But then 2020 came, and what was supposed to take a few more years had to happen within a matter of months. Data show that we have leapt five years forward in consumer and business digital adoption over this period.
Most businesses ramped up their digital transformation efforts to meet the sudden disruption in work and business ecosystems. According to Dell’s Digital Transformation Index 2020, which surveyed more than 4,000 global business leaders, eight in 10 organizations fast-tracked their digital transformation programs in 2020.
It has become clear that technology is no longer an option in this brave new world; it is a fundamental business requirement that needs to mesh into every part of the organization. Transformation can improve collaboration within and between organizations, customer engagement, promote higher employee innovation and productivity and present more accurate data insights. All these factors help companies to grow and put them on the front foot in a post-pandemic world.
How to improve your processes
Let’s take a look at how to kickstart your process improvement efforts:
- Start with a comprehensive strategy
Digital transformation impacts the manufacturing landscape on a scale last seen when Henry Ford introduced the concept of mass production. The difference is that manufacturing companies are using technology to move from mass production to customized production – at a rapid pace.
To move toward a digital future, organizations need to have a clear vision with an elaborate digital transformation strategy. It’s a complex process that requires significant investment that comes with risks.
The following five steps will guide you:
1. Analyze the market
This step is essential for creating a relevant and up-to-date strategy. You need to be aware of rapid industry changes and technology development to inform your strategy. It may even require you to go beyond your industry and explore success stories in other verticals.
2. Create a vision
Rather than only looking at the problems you’re trying to solve with digital innovations, focus on your long-term goals. Concentrate on the experience you want to create for customers and employees alike, without losing sight of reality. Build your strategic vision on the short-term objectives and resources you have available at present while focusing on your competitive advantage. Identify gaps in the current set-up and create implementation road maps to optimize it.
3. Design the digital experience
Most business leaders believe that their business’s success depends on customers’ digital experience, so pay special attention to the experience you want to deliver. Consider questions such as:
-
- What value can we provide to our customers?
- Is it convenient for them to interact with us?
- How can we change the way employees engage in business processes?
Consider how employees can do their tasks faster and easier with a new app, software, or digital platform. The primary focus is not on the new technology itself but the experience it can provide.
4. Assess the current state
As a business leader, you need a good understanding of your existing business processes and the new processes you want automation to enable before implementing the technology. Therefore, examine your digital infrastructure and analyze how well these tools address your current and future needs.
Identify areas where you’ll need to develop new functionality and the required integration to bring it all together. This evaluation will help you discover what specific technology to update, which process to automate or optimize, and what digital tools you should change. This will help you prioritize the efforts and investment needed for your process improvement strategy.
5. Prepare and adjust your infrastructure
As a first step, it is necessary to identify and surround yourself with a dedicated group of digitally savvy experts to ensure a successful transformation. If you can’t have an in-house team, find a reliable partner to implement the improvement strategy for your company effectively. Next, help your team develop skills needed for future changes with the appropriate training. It’s critical to make digital transformation part of the organization’s DNA by building a new digital culture that would align with the transformed business processes.
- Review and update standard work at all levels
In many companies, the level of process knowledge and understanding is often low. The company may have collections of standard operating procedures, but they are often poorly documented and outdated. Each employee typically follows their understanding of best practices.
Instead of individual employees using their knowledge, talent and creativity to perform tasks and process sequences in often counterproductive ways, they can invest their collective energy in a more valuable pursuit of process excellence. For instance, plant processes generate data that serves as input for digital lean, but accurate and continuous data will only materialize if processes are performed with standardization and discipline. Failing to do so would diminish the impact of a digital lean initiative.
Working with high-performing employees to challenge and improve the process, and embed this into automation will ensure significant improvements in the processes being automated. It will also reduce process problems across other parts of the business.
The same applies to leader standard work (LSW). With the rapid pace of technology development, there is little reason to believe that what worked for leaders in the past is likely to keep working in the future. As a result, traditional LSW is fast giving way to digital LSW. Digitized LSW lends itself to quickly compiling and analyzing data, allowing leaders to focus on the most critical needs and opportunities to improve.
However, for leaders to make effective decisions, they need to model the right behaviors so that strategic priorities flow rapidly down the organization and intelligence about the business quickly flows up. That’s why LSW is so essential for executive leaders, especially when it operates on a digital platform.
- Sustain improvements in the long term
Up until recently, process improvement initiatives often happened in pockets and not across diverse operating systems, which yielded only mildly impressive results. Functionally focused project efforts and silo thinking made results unsustainable and not inclusive enough to achieve overall business performance improvements. The process improvement efforts were also not managed from the top down.
To sustain improvements in a digital factory, organizations need to develop and nurture these digital capabilities:
-
- Diverse expertise and skillsets, such as data science, data engineering and product design – leaders should decide which roles can be filled by retraining and reskilling existing employees, and which should be outsourced or hired.
- Agile working – agile ways of working present a fixed timeline, cost and resources, but with little or no boundaries on completing a particular task or project. It allows organizations to learn, iterate and improve quickly.
- Data literacy – as digital operating systems present more and more data, the ability to understand, analyze and leverage data in decision-making becomes critical.
- Analytical reasoning – digitization is a continuous process that will require leaders and their teams to break down problems, analyze patterns in data, leverage new kinds of data, and continuously find different solutions.
- Next-gen technology – engagement with cloud and other technologies increased significantly during the pandemic. While many organizations have found IoT to be helpful for worker safety, such as determining if social distancing is being observed, they will continue to use it for remote operations, connecting with customers, and improving supply chain efficiency.
Automation plays a significant role in process improvement because it’s easiest to eliminate manual work and reduce human error. Process automation helps organizations understand where they need to improve and what is working as it should.
- Replicate successes
Replicating successes – known as yokoten in lean terminology – is accomplished by sharing information on effective practices and the problems they were designed to address. You can leverage the key lessons from your successful project in other functions or apply the same solution to an identical issue on a sister plant or site.
Replicating a successful project – rather than starting from scratch – offers enormous benefits. Whether digital or manual, these secondary projects are faster to identify root cause, carry less risk, and are generally quicker to complete, which means an increased return on investment. However, it’s important to not simply copy a practice from elsewhere, but to “go see” the situation in which it was developed and then adapt the practice for your own situation.
To entrench the habit of good project replication, apply these actions:
-
- Make the project leader responsible for replication opportunities as part of the original project.
- Identify potential future replication opportunities early on and contact the relevant line mangers as stakeholders. Keep them in the loop as the project goes on so that they feel comfortable with the proposed improvements.
- Provide governance oversight to your continuous improvement program by making the steering committee or project champion accountable for replicating successful projects.
- Ensure the project is fully documented so that all the key takeaways are available for others to use and build on.
By performing these and the preceding steps well, you will increase the payback from your process improvement initiatives many times over.
Download the brochure TRACC Leader Standard Work App and find out more about standardizing leadership practices across the global organization.
