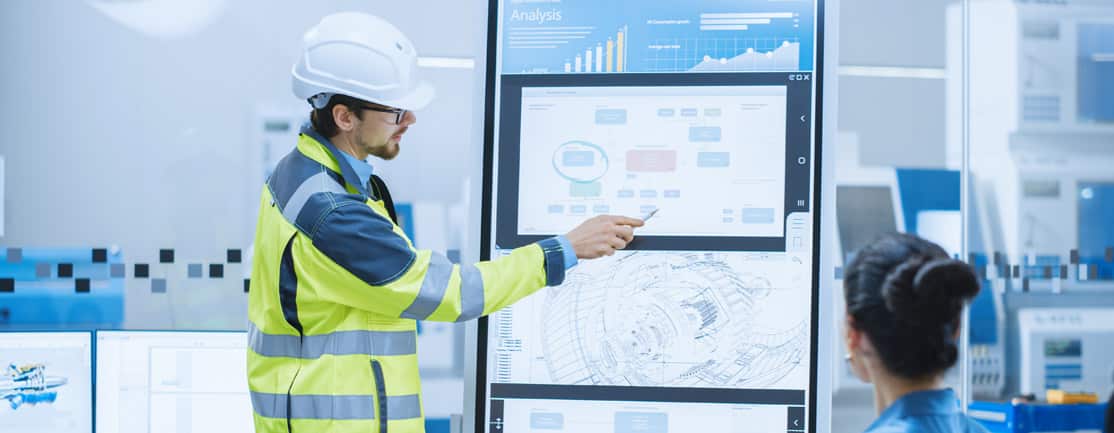
How to achieve operational excellence in the digital age
In today’s digital world, forward-thinking executives are increasingly viewing operational excellence (OpEx) as a key driver of top-line growth, and no longer as just a tool for incremental process improvements at an operational level. They understand that OpEx project teams and processes are best placed to create disciplined frameworks to gain a competitive advantage. As a result, they’re starting to align operational excellence teams at the strategic, value creation and customer experience levels to enable end-to-end business transformation.
What is operational excellence?
Operational excellence isn’t simply about the application of lean and continuous improvement principles – it’s a holistic culture change where all employees are empowered and driven to execute the organizational strategy in the most efficient, cost-effective way. Teamwork, problem-solving and growth underpin this continual drive for excellence, with a focus on improving processes and creating more value for customers.
A key requirement of operational excellence is having highly skilled and capable people who can solve problems quickly and effectively. Teams need to be guided by rigorous processes and standard work that ensure consistent, high-quality output. At this level, teams are motivated to identify new ways to create value across the operation, whether it be through increasing capacity, improving performance, or innovating both products and processes.
The only proven way to build this internal capability is with a focused operational excellence program that integrates people, processes and performance. This starts with establishing a clear plan of what needs to be delivered, then aligning an improvement program to develop people and the ways of working (processes) to meet these objectives.
In times of crisis, for example, during the coronavirus pandemic, operational excellence practices can add speed to daily routines, and value to emergency planning and preparedness. This may include assessing and resolving critical capacity and root cause constraints, rapid implementation of daily management systems to ensure visualization and fast decision-making, and standardization of practices and routines to ensure speedy replication and adoption throughout the business. Above all, clear leadership and coaching of staff are paramount.
Operational excellence as a driver of competitive advantage
The constant pressure from new competition is a major incentive for many organizations to refine or invest in their operational excellence methodologies. There is now a real need to instill a culture of continuous improvement to remain competitive in a highly competitive global market. This is clearly reflected in a report released by Proqis, titled The Global State of Operational Excellence: Critical Challenges & Future Trends. In it, almost 30% of survey respondents cited the threat of new competition as a key driver of operational change.
The report identified four other top drivers pushing change in the operational excellence ecosystem. These include:
- Customers’ needs — the ability to connect with customers, both internally and externally, is now almost ubiquitous; it’s easy to learn, seamless and intuitive
- Need to reduce cost — organizations are facing corporate-driven targets in cost and working capital reduction in an attempt to offset declining revenue
- New technologies — companies are scrambling to keep up with the latest technology, but these solutions are worthless without the right organizational culture and guiding principles to make the most of them
- Cross-industry disruption — startups and technological innovation are making the market more competitive every day, across all industries
Operational excellence and continuous improvement
A sustainable operational excellence strategy requires, an organization to follow an integrated approach to continuous improvement. This allows it to embed operations excellence in the very fiber of the business, rather than treating improvement as a disconnected set of projects and standalone metrics. The integrative improvement system can be defined as a standardized system that simultaneously and interdependently drives operational improvement across all functions and processes – and it provides a codified road map to do this. It requires three key structural components:
- Maturity- and process-based transformation
Transferring process improvement ownership from technical experts to frontline teams requires structural reorganization around lateral processes. A maturity-based management system needs a three- to five-year execution road map and must be capable of tracking maturity in terms of delivery. A shift in leadership style from ‘‘cop’’ to ‘‘coach’’ is also necessary.
- Functional integration
The upshot of an integrative approach is an organization primarily designed around processes, products, and customers, not functions. It ensures that functional improvement requirements (e.g. planning, procurement, IT, quality, maintenance, HR) and the improvement methodologies used are on a common platform and executed simultaneously, in concert with one another.
- Sustainability through a three-tier system
Sustainable improvement does not result from the mere application of improvement tools and processes. The introduction of lean, Six Sigma, Kaizen, autonomous maintenance, one-point lessons, 5 Why problem-solving, visual management, etc. are not sustainable without supporting systems and underpinning management principles. Sustainable change requires a three-tier system – management principles, operating systems, and tools.
Where does the OpEx journey begin?
The quest for operational excellence is often hampered by the lack of a well-planned and defined action plan for improvement that is consistently and constantly being executed. As a result, some functions in an organization are often in opposition to one another and operate in a way that makes meaningful business performance improvement near to outright impossible.
To help uncover potential divisions and differences among your managers on key issues of beliefs, values and vision, ask the entire leadership team the following seven questions, and then have an open discussion:
- What specific customer satisfaction improvement action items need to be initiated immediately?
- What measurable results and KPIs must be achieved and when?
- What specific business process improvements will we achieve over the next six months (or 12 months, 18 months, 24 months)?
- In what three areas have we achieved breakthrough business results?
- What five immediate actions are required to initiate, invigorate or enhance our operational performance?
- Do we have clear, time-phased, measurable objectives for operational performance improvement, and is accountability clear?
- What outside consulting assistance is needed to assist our organization to achieve business goals more speedily?
While an immediate, easy consensus is unlikely, the process of thinking, discussing and reaching a conclusion is, in itself, a good learning experience and a major advance toward an essential singleness of purpose and vision for the entire team. After successfully working out solutions to the preceding questions, the management team should have a common, agreed-upon operational direction.
Tactical objectives and action plans
A vision that is born out of a collaborative, careful and intelligent process is more likely to be successful. It is also important to translate and convert the underlying principles contained within the vision into a meaningful and impactful set of statements that can be communicated constantly and effectively.
To create a shared vision, you need to analyze your current situation and reach a better understanding of your company’s strengths and weaknesses as well as the various factors that affect the company’s performance.
No strategic plan in and of itself can help an enterprise change and move ahead to capture more market share, improve products and processes, increase customer satisfaction, or whatever is recommended within the context of a strategy. Effective strategic business planning requires a dynamic, methodical process that keeps the organization focused on the right issues and actions.
The very essence of planning operational objectives effectively is a continual process of ensuring that operations is consistently doing the ‘‘right things right’’. Connecting strategy to operations involves defining an operations strategy and translating that into tactical objectives and action plans.
Defining the right objectives and developing and implementing the ‘‘right’’ action plans are the focal points of an effective planning process. And here you need to be very specific with objectives, such as decreasing order-to-delivery cycle time (lead time) by a specified minimum amount, introducing a specific product at a certain target price, decreasing costs by a certain percentage, and/or reducing inventories to a specific level.
The next task is to define the action plans you’ll need. For example, you could plan to redesign the process of information and material flow to reduce order-to-delivery cycle times by 60% over the next six months, or introduce a methodology to decrease inventories by 35% in six months. Action plans need to define the what, who, why, where, when and how.
Action plans can integrate operations with business strategy and they can provide a practical focus for shared vision. They can do this in several ways, including:
- Traversing silos within the organization
- Minimizing tunnel vision
- Providing a structure for solving problems
- Encouraging people to think creatively in developing solutions
- Providing a methodology for conflict resolution
- Establishing common values and beliefs across the organization
- Creating a way for everyone to get on the ‘‘same page’’ and rapidly move forward
Change management steps to guide your operational excellence journey
The journey towards achieving operational excellence typically begins with an initial step change improvement, followed by continuous incremental advances. The implementation journey itself runs through a change management process which consists of the following four steps:
- Build the business case for operational excellence
To ensure the building of sustainable advantage across your end-to-end value chain, you’ll have to consider developing an integrative improvement capability as mentioned above. The upshot of an integrative approach is an organization that is primarily designed around customers and products, not functions. This ensures that both functional improvement requirements and the improvement methodology used are on a common platform, and executed in concert with one another.
- Integrate sustainability into the vision, strategy and objectives
Sustainable implementation requires that continuous improvement tools integrate into an operating system and are bound by clear management principles within a complete framework.
- Manage risks, reduce cost and build stakeholder value
Value generation and the reduction of operational risk are closely related to the culture on the production floor. Organizations that succeed in creating a proactive risk culture can use their strength to optimize the flow of value through an operational excellence culture.
- Develop competencies and support cultural change
Integrate skills development and improve the way work is performed throughout your organization by building the required skills at leadership, operational and production floor level. Build a learning and development strategy to ensure your workforce has the competencies required to deliver on the business imperatives.
Once you’ve defined the reasons for cultural change, convey them to the workforce. An organization-wide sense of urgency is necessary to compel the organization to transform. This is often referred to as being the ‘‘burning platform for change’’.
DOWNLOAD How-To Guide: Managing Change across the Organization to find out how to successfully lead and manage your change efforts.

Operational excellence and digital transformation
Manufacturing is going digital. Smarter robots, 3-D printing, big data, machine-to-machine communication and mobility are all part of a wave of converging technologies heralding the advent of the next industrial revolution. For manufacturers, this transformation is yielding a variety of new tools designed to build smarter factories and, lean manufacturing systems, to develop ground-breaking products, materials and techniques. At the same time, manufacturing companies are becoming more complex and globally dispersed, accelerating the need for increased innovation, collaboration and visibility. Manufacturers therefore face unprecedented challenges as these global economic forces drive competition and open opportunities in new markets.
These organizations need to become more efficient, flexible and collaborative to keep up with rapidly changing demands. CEOs recognize that to achieve these business objectives, and be competitive in a global manufacturing environment, their organizations need to do a better job of getting the right information to the right people at the right time, in an integrated format in order to make better decisions. The organization must become more responsive to changing market and operational conditions, without sacrificing efficiency.
Fundamentally, an incremental, maturity-based approach to operational excellence prepares the organization to adopt and adapt new technologies at the correct pace. The journey to Industry 4.0 is different in every organization and likely to evolve as new technologies emerge. Below are some of the fundamental capabilities your organization needs to develop — across every stage of the digital transformation journey — to ensure long-term success.
Stage 1 is characterized by silo thinking and little synchronicity between supply capability, market demand and product innovation. Stage 2 is where the transformative work begins.
Stage 2 – Internal Alignment
- Data management capabilities to capture accurate and usable data needed for big data analytics
- Standardized systems, such as an Enterprise Resource Planning (ERP) system, Quality Management System (QMS), Computerized Maintenance Management System (CMMS) and Manufacturing Execution Systems (MES), to support interconnectivity
- Identification of new skill sets managers and operators need to develop in order to use the new technologies
- Focus on implementing lean principles to minimize waste and overproduction and improve agility
Stage 3 – Functional Alignment
- Standardized and wide-scale big data and predictive analytics, business intelligence reporting and virtual environments
- Systems integration within the site, such as MES, QMS, Warehouse Management System (WMS), Transport Management System (TMS), and ERP, and with other key sites
- Selective introduction of mobile, wireless, telemetric, cloud-computing and sensor-based machine technologies to support automation and visibility
- Introduction of additive manufacturing (3D printing) where appropriate
Stage 4 – Value Chain Alignment
- Implementation of autonomous decentralized systems and artificial decision support
- Connected machines and systems that enable remote monitoring, diagnostics and maintenance, and dynamic calibration; and automated changeovers and quality checks
- Systems integration with key partners’ systems that enable automated replenishment
Stage 5 – Network Alignment
- Use of advanced prescriptive analytics, automation and machine learning
- Realization of autonomous factories
In an increasingly digital world, manufacturers seeking to optimize their operations need to understand the interplay between traditional continuous improvement and Industry 4.0. Valuable synergies can be generated by implementing CI and Industry 4.0 technologies in an integrative manner, rather than independently or sequentially. By taking an incremental, maturity-based and integrative approach to operational excellence, organizations will be able to adapt to new emerging technologies at the correct pace, and ensure that the right systems, processes and capabilities are in place to capitalize on the opportunities the digital era is set to deliver.
Competitive advantage today and in the future will come only by transforming your business from end to end, function by function and process by process. Following an integrated, cohesive approach to value generation will give you the edge on your competitors, even through times of economic uncertainty. As demonstrated by some of the world’s most successful corporations, operational excellence is both achievable and sustainable — it just has to be tackled the right way.
Contact us to find out more about how TRACC can help you power your journey to operational excellence and achieve sustainable results through best practice and work process improvement.