TRACC-powered Rapid Best Practice Deployment program turns the tide for Cargill flagship corn milling site
The remote town of Eddyville in the Midwestern US is home to one of Cargill’s key corn milling sites. As one of the largest players in the corn processing industry, Cargill views production optimization as a key focus.
Historically, the Eddyville site had been a leader in its division often and served as a benchmark for the other division sites. So, when profitability and KPI performance started dipping at the Eddyville plant, management instituted a TRACC-powered Rapid Best Practice Deployment program to stop further deterioration.
By refining employee engagement and leadership behavior, revising several KPIs, and focusing on frontline capability building, the Eddyville site managed to turn the tide within the six-month rapid deployment period.
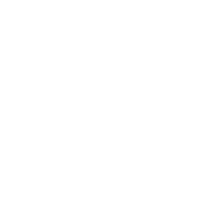
- More than US$700,000 realized in project savings following the implementation of the Rapid Best Practice Deployment program
- Moved from bottom of divisional standings to nearing the top within six months
- On track to achieve 150% of their normal target
- Strong project governance contributed to successful deliveries
- Active projects currently valued at more than US$7 million in potential savings
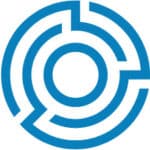
As a leading purchaser and processor Cargill is committed to sourcing sustainably produced corn in major supply chains worldwide. Part of this commitment is to work on continuous improvement in areas that are relevant for the farmer, customer and the environment. While the Eddyville plant already had several improvement projects in place, there were too many competing priorities, no project sponsors, and project leaders who didn’t fully understand their roles. In addition, there was a lack of support for these projects.
So, when performance at the Eddyville plant started faltering, plant management had to act quickly. They were looking for a structured process to improve accountability, project execution, KPIs, and shop floor involvement.
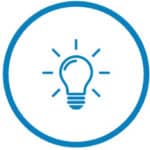
To ensure a quick turnaround, plant management focused on the rapid deployment of the TRACC Value Chain Improvement Solution. Once the Daily Management System was in place, Implementation Task Forces (ITFs) were established for the Visual Management, 5S, Teamwork, and Focused Improvement best practices.
Following a climate survey early in the implementation process, culture focus groups were introduced to 25% of the workforce with representative demographics. Where appropriate, additional ITF workshops were added to the training schedule.
The next step was to reduce the overall number of legacy projects and training the project leaders in the use of the project notebook in TRACC. Project sponsors also received thorough training in project governance.
The primary focus areas of the Rapid Best Practice Deployment program included operational performance, behaviors and mindsets, and manufacturing practices. The TRACC foundation best practices (Teamwork, 5S, Focused Improvement, and Visual Management) were implemented to focus on frontline capability building, while operational performance was addressed via profit improvement projects (PIPs) and regular control loops. With TRACC as the backbone, a fully integrative improvement system was developed and owned by all employees. Not only did this ensure sustained results, but the team’s efforts gained recognition across the broader group. In fact, plans are afoot to introduce similar TRACC-powered best practice deployment initiatives elsewhere in the Cargill group in the near future.
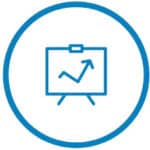
Within six months, the Eddyville plant moved from the bottom of the divisional performance standings to nearing the top. Following the rapid best practice deployment, more than US$700,000 were realized in project savings, while active projects currently represent more than US$7 million in potential savings.
Studies conducted by the project sponsors revealed that even with a reduced number of projects, the output was higher. This was due to better adherence to the DMAIC process and faster execution through proper governance.
As the PIPs and project governance took hold, the entire mood shifted across the plant following successful project deliveries. Improved interdepartmental teamwork and workforce empowerment became clearly visible. As a result of the improvement work done, the plant was on track to achieve 150% of their normal target.
Cargill Inc., one of the world’s largest agribusiness corporations, is a privately held business with diverse product lines and processes from steel production to grain milling to commodities trading. With more than 150 years of experience, Cargill currently employs 160,000 people in 70 countries.
This resource has been prepared for general guidance on matters of interest only, and does not constitute professional advice. You should not act upon the information contained herein without obtaining specific professional advice. Competitive Capabilities International (CCi) does not accept or assume any liability, responsibility or duty of care for any consequences of you or anyone else acting, or refraining to act, in reliance on the information contained in this resource or for any decision based on it.