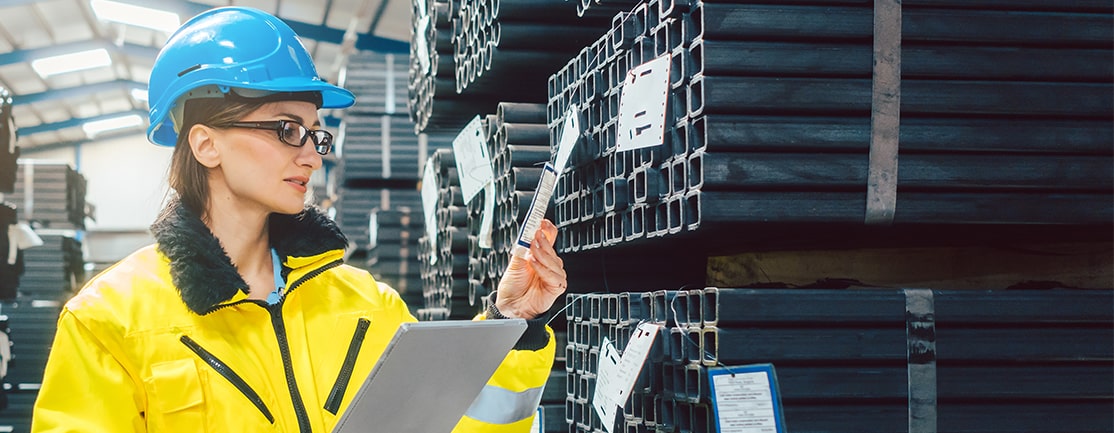
The death of single sources of supply
There’s no disputing that COVID-19 has had a devastating impact on lives and economies across the globe. While we have faced mega disasters before ― the Fukushima earthquake and subsequent tsunami in 2011; and, going further back, the 1918 Spanish flu ― none of these black swan events disrupted global supply chains to the degree that COVID-19 has.
One much-debated practice that has become more prevalent in business over the years is the concept of ‘single source of supply’. This concept, in my opinion, has been incorrectly viewed as a core component of Lean. Lean firmly places the primary focus on the customer, invests in people, and builds on the integration of different organisations within the value chain to ensure both excellence in the final products and services, and fast response capability. Plus, the razor-sharp focus on waste allows this to be done at the lowest cost.
While this has apparently led many organisations to standardise single supply sources, this practice appears to be an unfortunate by-product of low-cost focus at the expense of understanding the risks. Toyota, who are most often held up as the ‘lean architects’ because of their Toyota Production System (TPS), embrace their extended network of partners and suppliers by challenging them and helping them to improve (Principle 11 of The Toyota Way by Jeffrey Liker). But this principle is all about partnering, not exclusivity.
Firstly, a definition for the purpose of this article:
- Single source of supply is the result of a conscious decision to only source from one supplier though multiple suppliers are or could be available
- Sole source of supply is when that supplier supplies a unique product or service. There is no other business that could supply that product or service. If this is the case, the choice is not a choice, but this arguably increases the risk
It is both the integration of the value chains upstream to suppliers, and the never-ending drive for low cost that has meant many organisations have embraced single sourcing as the solution. The advantages of single sourcing are clear:
- Less work in qualifying suppliers
- It’s easier to collaborate with a single supplier on the next design or on improvement opportunities
- Being able to leverage the lower costs that come with higher volumes
- Transparency up and down the value chain
But this should be countered by the significant risk:
- A catastrophic event could affect the supplier
- Other suppliers may lose interest in supplying, or even in being a back-up
- When supply is tight in the whole market, the buyer may be disadvantaged in sourcing from alternative suppliers
It is this risk component that is being highlighted now with the COVID-19 pandemic. Because historical data on these rare mega disasters is limited or non-existent, their risk is hard to quantify using traditional models. As a result, many companies do not adequately prepare for them. This can have catastrophic consequences when they do strike. Read this blog post for more insight into how organisations can identify, prevent and mitigate risk in times of crisis.
Organisations are hastily reassessing their need for an integrated supply chain continuity plan. Single supplier sourcing is just one component that should be considered. Questions that need to be answered are:
- Which supply chain risks must be managed?
- How much risk is acceptable?
- Who is responsible for these supply chain risk management activities?
In the HBR article entitled Coronavirus is proving we need more resilient supply chains a practical approach is presented to managing sourcing risk. See the table below:
A Practical Approach to Managing Sourcing Risk
Use revenue impact and risk of supply disruption to prioritize supply chain resiliency measures. | ||||
HIGH REVENUE IMPACT if supplier or part(s) is lost |
|
|
||
LOW REVENUE IMPACT if supplier or part(s) is lost |
|
|
||
Two or more sources are qualified. | Two or more sources are qualified, but all business is routed to one supplier. | Alternate source is available but needs to be qualified before using. | No alternate source is available or possible. | |
LOW RISK OF SUPPLY DISRUPTION | HIGH RISK OF SUPPLY DISRUPTION | |||
Source: Resilinc | © HBR.org |
This same article recommends that “at a bare minimum, companies should invest in 24×7 monitoring of their global suppliers … In the first few weeks of January 2020, companies that had mapped their supply chain already knew which parts and raw materials were originating in the Wuhan and Hubei areas and, as a result, could bypass the frantic hunt for information and fast-track their responses.”
By implication, businesses that only had a single source of supply out of Wuhan, had to reconfigure their supply chains, while those with multiple sources were better placed to make alternative arrangements. Coming back to Toyota, one of their core policies is to source any critical part from multiple geographical locations; read this blog post by Jeffrey Liker for further insights.
So, is the single source strategy dead? Yes, it is. COVID-19 has demonstrated that the risks outweigh the returns, especially with respect to geographical location of suppliers. Ensure you have at least two for each strategically important supply, and that they are geographically separated.