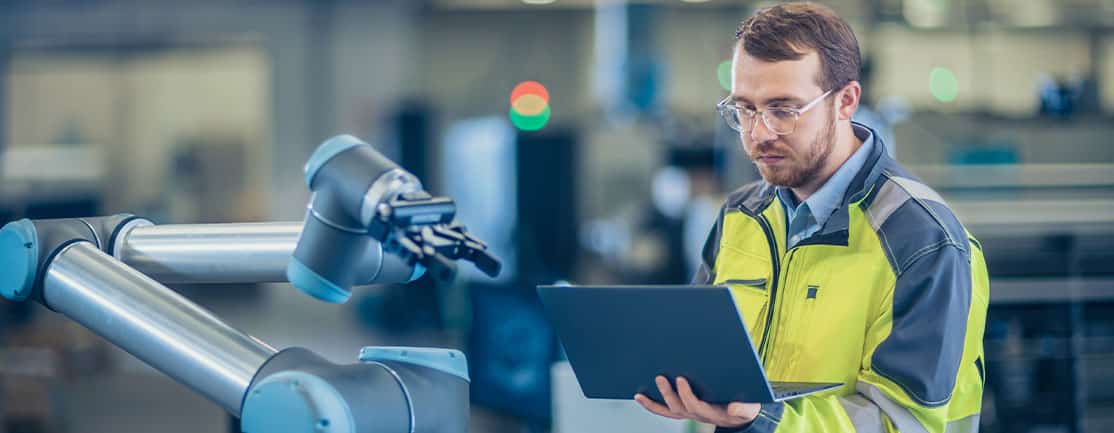
Continuous improvement: The engine of next-generation production systems
Continuous improvement (CI) is a widely accepted scientific approach to process enhancement and waste reduction. However, as manufacturing enterprises start to migrate to a digital future, a new approach to continuous improvement will be required for organisations to remain relevant. In a recent interview, CCi CEO Glenn Leask and CCi Products Director Geoff Schreiner discuss continuous improvement and why they see it as ‘the engine’ of next-generation production systems. They explain how organisations can leverage the key tenets of continuous improvement while embracing the shift to a digital world.
What is continuous improvement, and what are the continuous improvement practices and principles traditionally used in production systems?
Continuous improvement is an organisation’s incremental and continuous efforts to improve all aspects of production. It pertains to large, ongoing projects as well as shorter ‘quick wins’ such as Profit Improvement Projects (PIPs). Improvements are implemented and their impact is measured. Successes are often shared to inspire greater engagement in the continuous improvement cycle.
Continuous improvement efforts usually aim to achieve one or more of the following:
- eliminate waste
- reduce cost
- reduce lead times
- improve quality
- improve flexibility and responsiveness through streamlining all processes
Continuous improvement succeeds best when it is integrated into the culture of the organisation, and all employees – not just management – take responsibility for improvements. Everyone is a problem-solver, both in terms of job requirements, and skill and experience. This problem-solving ability, applied by all people to all aspects of their work as a standard, normal part of the work results in employees continually identifying and executing improvement opportunities.
Integrative improvement is a comprehensive business improvement approach that:
- arranges an organisation around end-to-end processes that serve customer segments rather than functions.
- involves all employees in improving processes and systems.
- ensures committed leadership that actively encourages the right mindset and behaviours to support integrative improvement principles so that it gets embedded into the culture of the organisation.
Traditionally, high-performing organisations have infused their production systems with lean, continuous improvement and performance standards to drive efficiency and bottom-line results. It paid off ‒ by making continuous improvement and standard work a business priority, these organisations consistently delivered superior performance.
Why is continuous improvement important in a digital world?
To thrive in the digital age, organisations need to continually monitor and adjust processes to ensure greater efficiency, productivity and competitive advantage. It is this relentless focus on process excellence that lays the foundation for a successful digital transition.
New digital technologies are helping to identify untapped efficiency opportunities and have the capacity to unlock unprecedented levels of productivity and innovation. Only organisations that place a premium on continuous improvement practices and principles will be able to leverage these benefits.
The digital era demands greater levels of agility and collaboration – against this backdrop, continuous improvement can be viewed as the ‘launch pad’ that helps organisations achieve these ambitions and prepare for the future world of work.
According to global research and advisory firm Gartner, corporate production systems are now considered mature and mainstream. What is the next-generation production system, and what are its objectives?
Next-generation corporate production systems, known as digital operating systems (DOS), are aligned with the supply chain’s operating system and are designed to harmonise lean and continuous improvement practices and principles with smart manufacturing.
While DOS won’t change corporate production systems’ fundamental purpose, they will transform the way they are built and run. DOS integrates the application of technologies and digital deftness with lean and CI practices and principles to drive competitive advantage across the end-to-end value chain.
Download the white paper Digital operating systems: The next-generation of production systems for the building blocks of a successful transition to DOS.

Why is it important for organisations to start looking at implementing digital operating systems now?
Companies can no longer ignore digital disruption. Yesterday’s innovation is today’s mainstream and today’s cutting-edge is tomorrow’s mainstream. Right now, organisations should have cloud capabilities, rigorous data analytics and some interoperability between information (IT) and operational (OT) technologies.
Traditional production systems tended to be manufacturing focused and didn’t take the full extent of the supply chain into account. This historical model is becoming outdated, mainly because it limits the interconnected fluidity and agility required of today’s value networks, which DOS promotes.
Manufacturing organisations that adopt new operating systems and associated technologies, as well as an agile approach to continuous improvement, can develop new ways to improve efficiency and scale solutions across the entire business. They can then build true competitive advantage.
How will a company know if they are ready to start implementing a digital operating system?
Research shows that organisations in higher digital maturity stages achieve nearly 50% better revenue growth than low-maturity companies, and third better than those in the middle stages of digital development.
A digital maturity assessment will reveal the company’s current baseline state and highlight key focus areas, which will assist in mapping out a DOS implementation process that focuses on adopting new technologies and processes at the right pace.
Organisations that have succeeded in achieving breakthrough performance have one thing in common: they moved systematically through the stages of best practice maturity to build the foundations of sustained performance improvement.
Digital maturity can be assessed by looking at eight key themes, which are outlined below. It’s also important to note that not all sites within a global organisation will have the same maturity level.
1. Strategy | Digital transformation should be prioritised and incorporated into the organisation’s business strategy and goals. Digital-first positioning requires deliberate, dynamic, and progressive planning. | |
2. Ecosystem | Digital platforms are increasingly leveraged to broaden external collaboration in the pursuit of enhanced customer value and end-to-end capability. As such, organisations need to assess the degree of the digital alignment and strategic partnerships across their network. | |
3. Leadership | For digital transformation to succeed, the organisation’s leadership must create a compelling vision of how the business will thrive in the digital world, which should also be reflected in the business model. | |
4. Design | Internal organisational architecture is increasingly reflecting a shift away from silos to agile operations. Technological tools and applications play a major role in improving this cross-functionality and in supporting an agile organisational design. | |
5. Data | Data, and its monitoring and assessment through appropriate analytics, can unlock insights and create value. Future-focused organisations will, therefore, gather as much data as possible and analyse it to inform business operations and increase competitiveness. | |
6. Technologies | There is an escalating scope for automation in manufacturing operations and business processes, including technology applications to support and merge enterprise systems. Lineside systems and Manufacturing Execution Systems (MES) will interlink more holistically, and interconnect with other business processes. The potential for big data analytics and advanced, real-time decision-making and execution will also become a reality as capabilities approach quantum computing.
Organisations undertaking a digital transformation journey should have a three- to five-year-plan for incorporating new technologies, including Artificial Intelligence (AI), into its operations. |
|
7. Innovation | The development of innovation goals, the establishment of digital innovation teams, and the company-wide use of innovation tools are signs of a maturing digital culture and, as such, should be made a part of the day-to-day operations of the business. | |
8. Capability | Talent must be enabled to perform. The digital workplace and factories of the future will require a new level of digital and technology skills, that must be updated continuously. This involves empowering workers to innovate with technology, managing talent development and implementing new ways of working. Some examples of effective learning methods include gamification of new skills, applying virtual or augmented reality, and delivering real-time work instructions via digital platforms. |
What should the key focus areas be when implementing a DOS?
Any DOS implementation strategy should be maturity-based. Once an organisation has determined its current state of digital maturity, it should define deployment phases (i.e. create an implementation road map), based on each site’s unique requirements.
This road map should include actions relating to:
- Skills and capability building: Equip and upskill workers to thrive in a technologically advanced manufacturing environment
- Process improvement: Put in place processes to support a digital factory and redefined standard work
- Standardisation: Standardise processes to replicate successes across the global organisation
- Technology implementation: Implement and optimise advanced technologies to drive efficiency
- Data and analytics: Develop and implement advanced, data-driven problem-solving techniques
How does TRACC support organisations in designing, running and optimising their digital operating systems?
The many benefits of migrating to DOS include access to real-time data, faster decision-making, E2E visibility and system integration. To capitalise on these benefits, organisations need to focus on three key areas: building a lean and continuous improvement foundation, developing skills and adopting new technologies. Migrating to DOS is a complex undertaking, which is made much easier with a DOS enabler, such as TRACC.
TRACC is a digital integrative improvement solution that is designed to support organisations as they transition towards DOS. TRACC’s proven methodology, technology and processes can help organisations:
- create a stage-based implementation road map that will govern DOS implementation across global sites
- develop digital capability and promote new behaviours and competencies across all levels of the organisation
- access role-based improvement work tasks within a responsive user interface (UI) framework
- correlate performance and practice data to identify trends for rapid decision-making
- enable predictive performance improvement driven by machine learning
Integrating the application of technology and digital deftness with lean and continuous improvement practices and principles – at the right pace, and through a digital operating system – leverages technology’s potential to unlock unequalled levels of innovation and productivity throughout the organisation.
Contact us to find out more about how TRACC can help you design your DOS and achieve sustainable results throughout your organisation.