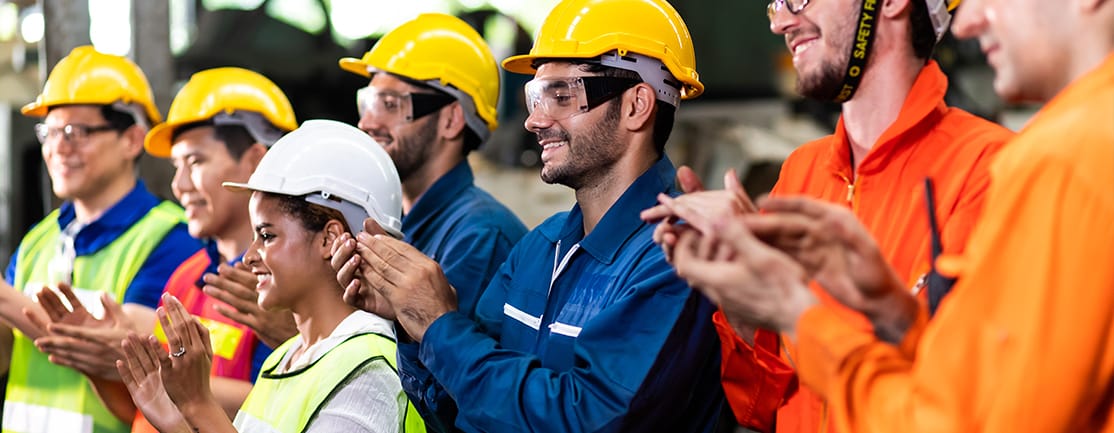
Why a continuous improvement culture is the bedrock of world-class manufacturing
A continuous improvement culture is about getting everyone engaged and involved in making small gains consistently. Here’s a look at the key characteristics and benefits of a continuous improvement culture, and why this is important for manufacturers and businesses across the globe.
An amazing mathematical equation proves the power of small gains made consistently: A growth factor of just 1% per day will result in a compounded measure of 37.78 times the starting number one year later. This is the principle behind developing a continuous improvement culture. It translates to many areas of human endeavour. A famous sporting application, for example, is how high-performance coach David Brailsford transformed the British cycling team from no-hopers to 2008 Olympic champions by eking out 1% improvement in every aspect of preparation – obvious ones like training and equipment, but also in nutrition, precautionary health and safety measures, and the disciplines of teamwork.
It works for manufacturing and production, too.
A continuous improvement culture is an age-old quest
Historians believe that the first mass, standardised production methodology was implemented by Venetian shipbuilders in the 1400s. Vital to protect the mercantile hegemony of the city-state, the Venice Arsenal could shift a completed and armed vessel through its production line in an hour.
Centuries later, and far more well-known, Henry Ford is considered the founder of standardisation processes for commercial purposes. Then, from the 1960s, Toyota pioneered and progressed a disciplined systemisation which has famously evolved into the Toyota Production System (TPS) or the Toyota Way – the foundation for lean, quality-geared production over the last 50-60 years.
At the heart of the Toyota Way is kaizen. Kai is the Japanese word for ‘change’, and zen means ‘for the better’. Hence kaizen translates simply as ‘improvement’. But the spirit of the word translates less easily: it is a deliberate, purposeful mission to make small but meaningful differences in a push towards operational excellence. In a workplace context, this requires that continuous improvement involves everyone, and encompasses everything related to the entire organisation.
Download the how-to guide: Driving employee engagement on the CI journey for tips and techniques to keep your employees involved and engaged on the CI journey.

Why is a continuous improvement culture important?
Culture: “the environment that surrounds us all the time, the shared values, belief systems, attitudes and the set of assumptions that people in a workplace share.”
Continuous improvement shifts the needle on the organisation’s people, processes and technologies by instilling leadership behaviours, improvement methods, and enabling technologies which, orchestrated together, are a purposeful force for iterative lean practices.
The minimisation of waste – in raw materials, other inputs, labour hours and inventories – and the optimisation of process efficiencies in quality-driven production are hallmarks of traditional production systems such as TPS or TQM, which foster a lean continuous improvement culture. Like the benefits of operational efficiencies, these are generally clear, tangible and evident to both factory workers and senior management. And cost savings inherent in continuous improvement programmes are often clear and measurable. Consider, for example, Unilever’s Sustainable Living Plan, intended to contribute to the circular economy by making all packaging reusable or recyclable by 2025. Launched in 2010, the ongoing initiative is credited with achieving over €1 billion in cumulative cost savings to 2020, partly by innovating lighter, cheaper packaging materials, and partly through improved energy and water efficiencies in the company’s production facilities.
Gains such as these are similarly palpable where continuous improvement initiatives manifestly refine processes or upgrade the quality of finished goods. Or, as an identified goal, when they boost productivity by creating greater output for the same inputs: labour productivity rates and overall equipment effectiveness (OEE) indicators will reflect whether, and at what pace, improvements are occurring.
The varying vectors of improvement
The benefits of a continuous improvement culture, however, run deeper. The kernel of genius within the philosophy of continuous improvement is that striving for excellence throughout the company’s supply chain creates more value, faster, in multiple ways – and in opposite vectors. So, insistence on quality improvements may require input costs to rise, but a premium sales price can more than compensate – and the quest can begin to find new, cheaper, yet even better raw materials, or to sharpen the production process.
One area of incremental gain enables others, as employees see the benefits of continuous improvement and are thereby motivated to improve further. Consider the performance impetus created by Paul O’Neill when he took over as CEO of loss-making industrial giant Alcoa (Aluminum Company of America) in 1987. O’Neill identified the company’s sub-par safety record as a direct consequence of its flawed systems and processes, and poor management. He believed he could transform the company by prioritising safety: “Focusing on worker safety can transform an entire organisation and dramatically improve culture, quality, productivity, communication, and ultimately profits,” he told shareholders at the first meeting of his tenure. “I intend to make Alcoa the safest company in America. I intend to go for zero injuries.”
He introduced small but important new safety procedures and protocols to be followed at the commencement of every job. Managers were held accountable for detailed task instructions, which had to include visual leader-boards with safety checklists. Quick improvements in safety systems led to incremental gains in labour productivity; better precautions contributed to improved machinery and equipment usage; material waste was reduced; inventory levels stabilised at more efficient levels, leading to improved customer fulfilment. Employees felt safer, and were more engaged – sometimes calling O’Neill directly not to report safety problems, but to propose improvement ideas of their own unrelated to safety, including innovations.
O’Neill had succeeded in creating a culture of continuous improvement within Alcoa. He understood that embedding continuous improvement culture and lean thinking within the organisation is a pathway to holistic enterprise development, including top-line revenue growth and future-proofing. Within a year, he transformed the company into profitability, and when he retired in 2000 Alcoa’s revenues were $1.48 billion, nearly eight times what they were when he started. Alcoa’s market capitalisation had skyrocketed from $3 billion to $27.5 billion.
What does a continuous improvement culture in manufacturing look like?
Alcoa’s transformation illustrates the profound, composite Return-on-investment (ROI) potential of a company’s continuous improvement culture. Still, given that culture can be difficult to pinpoint, even ephemeral, what are the major characteristics of a continuous improvement culture in a manufacturing entity – those distinctive ways-of-working that set it apart from others less driven to improvement?
Things are measured. | Indeed, almost everything is measured. From the monitoring of machine efficiencies, to warehouse picking accuracy to on-time customer order fulfilment rates: the inputs, outputs, flows and productivity of every part of the value chain is checked and assessed. Knowing how things are tracking is the basis for accountability. |
Data is appreciated, and used, diligently. | Data-centricity goes hand-in-glove with a culture of daily continuous improvement. Machine metrics, automated data gathering, powerful analytics and modelling tools combine to garner deep insights and drive incremental gains. Smart manufacturers incorporate data into every aspect of production and the supply network, and seek to master it towards a constant push for greater value creation. |
Standards are regularly revised. | Standards are not only crucial for consistency, but they are also intrinsic to kaizen. Without standards, gains cannot be tracked, nor new benchmarks set – without which improvements are unsustainable. Think of world records in athletics: They drive each generation of athletes to go faster, higher, longer – and when a record is broken, that inspires the next generation. Without the record-keeping of new standards and milestones (or lack of continuous improvement culture), stagnation would occur. |
Information is prominently displayed. | Linked closely to data-centricity is the real-time sharing of, and attention paid to, relevant forms and formats of information. The awareness of statuses, the understanding of key performance indicators and their tracking, the knowledge that improvement starts with a sense of immediacy: These are encapsulated in visual displays such as digital dashboards and interactive smart- or white-boards scattered throughout the organisation. These are tell-tale signs that the figures and flows of production are constantly monitored and assessed. Transparent information is the bedrock of internal communication as well as end-to-end network visibility. |
Leaders are involved. | As part of standardising their own work, top and senior management will be seen walking around, conferring with team leaders, or asking questions of factory floor workers. They’re committed, and seek to understand nuances as well as specifics of processes, so they listen rather than lecture, and pay attention to concerns and ideas from the assembly line. Leaders seek to develop people through coaching rather than direction, knowing that problem-solving capabilities must reside predominantly among the people who do the work. And leaders recognise and celebrate success, inspiring their team members along the journey of continuous improvement. |
Employees are engaged. | People are ‘present’, motivated and – optimally, given excellent leadership – inspired. This is a powerful productivity driver: a study by Bain and The Economist Intelligence Unit measured a 44% productivity improvement by motivated employees compared to satisfied workers, and a 125% improvement made by inspired workers. A continuous improvement culture complements efforts to boost employee engagement because it instils the idea that an employee has two jobs: their work, and constantly thinking how to do their work better. |
No-one looks in the rear-view mirror. | When improvements and gains are realised, satisfaction is brief. The focus shifts yet again: How to do even better? What new problems need solving? What challenges may be coming around the next corner? And because capitalising on technology is woven into the fabric of a continuous improvement culture, smart manufacturers are also digitally-geared; their leadership is manifestly abreast of developments in robotics and artificial intelligence (AI), and ahead of the digital transformation investment curve. |
The perseverance of long-term winners
“To be built to last you must be built to change. Visionary organisations have a relentless drive for progress – change, improvement, innovation and renewal,” writes management and performance consultant Jim Collins in his book Built to Last.
Or perhaps the essence of continuous improvement is in thinking of its absence. Without a quest to keep improving, stagnation will occur. Competitors will take market share and new disruptors may make the organisation’s offering obsolete.
The late Steve Jobs, founder and CEO of Apple, once said: “I’m as proud of many of the things we haven’t done as the things we have done. Innovation is saying ‘no’ to a thousand things.” Churning, incubating and testing 999 ideas before finding that special one: That’s the epitome of a ceaseless ambition to keep improving.
Continuous improvement means that everything matters
Fundamentally, continuous improvement drives culture change. By definition, improvement requires the implementation of initiative. It keeps the organisation dynamic – not resistant to change, but willing and able to embrace challenges and the inevitability of yet further flux.
The crucial context is that technological advances have levelled the playing field. Competitive advantage is no longer guaranteed by size and scale alone: Even local or smaller manufacturers can drive deep degrees of competitiveness by leveraging technology and adopting the fundamentals of lean production.
So, today, leading organisations apply continuous improvement in extended ways. They seek benefits in customer service and satisfaction metrics, in innovation and time-to-market, in an inspired workforce displaying cohesive teamwork, discipline, knowledge-sharing and agility. The central principle of a continuous improvement culture, in this broader sense, is a state of preparedness to cope with challenges and to keep finding a better way – to do anything and everything.
Download the eBook The definitive guide to integrative improvement for more on this holistic and sustainable approach to continuous improvement.
