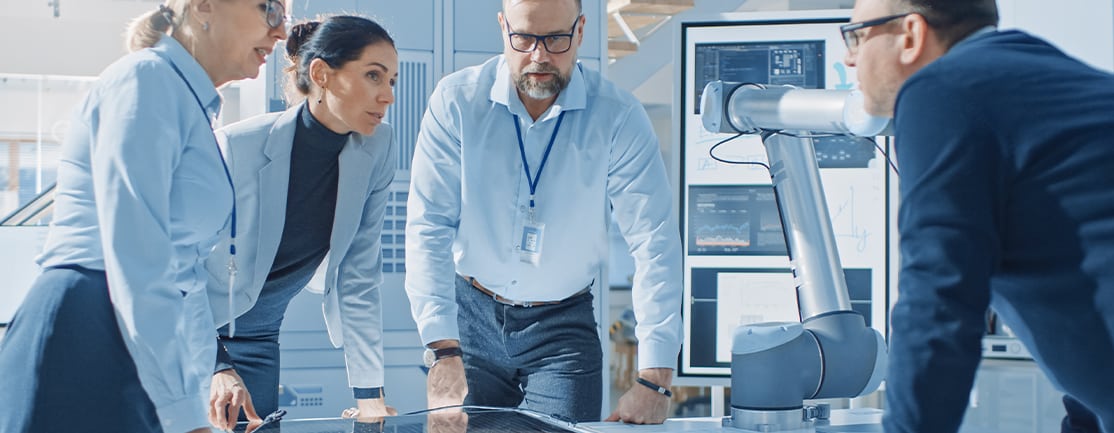
Digital transformation post-COVID-19: Sustaining gains and capitalising
COVID-19 has triggered a general, overwhelming understanding among CEOs that technology investments need to be stepped up. Here’s how manufacturers can strategise, sustain the gains and further capitalise.
A tipping point, according to culture and sociology writer Malcolm Gladwell, is the “moment of critical mass, the threshold, the boiling point, when everyday things reach epidemic proportions”. The definition seems apt in our COVID-19 impacted times. In many respects, the pandemic has forced organisations to transform or push the accelerator on digital transformation spending. It’s clear that digital transformation in manufacturing – as represented in digital operating systems (DOS), or next-generation production systems – is catalysing renewal.
One major global survey indicates that almost 50% of chief executives plan to increase digital transformation spending by at least 10% over the next three years. Research by Markets-and-Markets indicates the ongoing expansion of the smart manufacturing segment, per its definition, projected to hit $385 billion by 2025.
In its FutureScape: Worldwide Digital Transformation 2021 Predictions report, technology research firm International Data Corporation (IDC) notes that digital transformation expenditures are surging, and estimates a 15.5% CAGR between 2020 and 2023, with a three-year aggregated investment of $6.8 trillion.
But if the pandemic has been an inflection point for digital transformation in manufacturing, it’s also true that digital maturity is not a switch to turn ‘on’. It requires a journey, and many manufacturers – even leading, legacy producers – are in the process of building digital capability, and may require customised guidance to transform. Global food manufacturer Cargill Corporation, for instance, has emphasised the need to align and integrate operational and information technologies as a foundation for embedding its next-stage transition (read more on this in our recent white paper Digital operating systems: The organisational need for guidance). Like Cargill, many organisations will view OT-IT integration and convergence as a crucial initiative: Capitalising on the greater compatibility within Industry 4.0 technologies can secure production efficiencies, uncover customer insights, and blend these into meaningful value chain gains. Prioritising technology investments in this ambit will help sustain improvements and solidify the digital transformation.
More broadly, strategising a phased orchestration towards digital maturity assists in implementing sustainable change, and to fully capitalise – not only within operations, but for the entire business and across the extended value network.
Download the white paper Digital operating systems: The organisational need for guidance for a well-orchestrated strategy for DOS implementation.

3 key considerations to sustain digital transformation in manufacturing
Organisations should consider the following to capitalise on and sustain digital transformation gains post COVID-19.
Avoiding complacency
It is a reality of change – including rapid digital transformation in manufacturing – that plans are shown to be incomplete, flaws are revealed, and unforeseen problems arise. ‘Digital’ is itself a fast-evolving, multifaceted aggregation of technologies, ecosystems and platforms. Sustaining best practices is vital, and in the sense that the quest for improvement is ceaseless, there is an ongoing need for upskilling, learning, development, renewal and fresh cycles of change.
Feasibly, the haste to cope with COVID-19’s disruptions may have resulted in a suboptimal, fragmented DOS implementation. Digital maturity may be an illusion rather than reality – evidenced by under-delivery in certain aspects. Now is an opportune time to assess the organisation’s true digital status.
This will help to clarify alignment to key strategies (or refine strategic focus), highlight where competitive advantages or lags are occurring, and reset benchmarks for ongoing digital investment budgeting.
Assess your organisation’s digital maturity:
Re-evaluate strategy | “Strategy processes really are in the running for the world’s biggest zoo of frolicking biases and social distortions,” write the authors of Strategy Beyond the Hockey Stick: People, Probabilities, and Big Moves to Beat the Odds. One of the book’s main recommendations – given that strategy actually plays out according to real-world uncertainties – is to strategise according to probabilities. And to be adaptive in its implementation.The point is acutely relevant to digital transformation in manufacturing. Digitisation creates a new paradigm, and widens opportunities. But transformation – on top of pandemic-enforced changes to ways-of-working – is disruptive. Plan (and budget) on different horizons, and model adjustments for multiple scenarios. | |
Digital outlook | Manufacturers often embrace technologies for their newness, their promise. Global consultancy Gartner calls the tendency – as part of a wider affinity for apparent innovation – the ‘hype cycle’. Forerunners may grasp at the first green shoots, but the more committed organisations navigate through the cycle; they match new technology options to specific goals, and have a mindset attuned to a longer-term view. Digital is understood to be an enabler, not an end in itself. Evaluate whether the organisation’s strategies and objectives for digital are genuinely synchronised with the goals of the overall business. | |
Take a culture pulse | Even a rigorous change management programme may not, as yet, have been wholly successful. Solidifying change is significantly dependent upon employee commitment and engagement. A high-performance, digitally-orientated culture is a marker of digital maturity within the organisation, and a necessity for iterative, integrative improvement.Sustaining improvement and digital progression also depends upon leadership. Leader standard work (LSW) – a pillar of traditional Lean practices – may have become blurred in the transition. To sustain initiatives and engrain digital culture, leadership behaviours must be attuned to the orchestration of digital progression. | |
How’s your data? | Data-centricity is both a driver and a function of digital operations. Modern production systems gather, generate and use voluminous data; its value lies within automation, the forging of insights, the modelling of scenarios, and analytical assessments throughout the demand-driven value network. Data mastery is one of the pillars of smart manufacturing, and a fundamental requirement for sustained gains in a digital environment. | |
Scale the digital ecosystem | If the enterprise remains rooted in siloed, hierarchical, functionally-orientated organisational architecture, it is opportune to redesign. Capitalising upon digital’s advantages requires a 180-degree swing to flatter, fluid structures which align with, and liberate, the potential of digital systems and a digitally-enabled workforce. Now, too, is the time for collaboration, partnerships and new ventures in an expanded network. Even if the organisation, realistically, is not primed for M&A activity, elevating or fine-tuning the ecosystem may leverage further innovation and value creation. | |
Visibility and resilience | New technologies have a zero barrier to entry – all organisations have access to the same information and technology – which means the key differentiator in the digital age is not access to technology, but rather the ability to learn and adapt faster than competitors. Thus, organisational resilience is closely linked to its culture of problem-solving and continuous improvement. By enhancing end-to-end transparency, and further automating processes, digital technologies and systems also boost organisational resilience. |
Digital as a multiplier of manufacturing potential
The context for sustaining digital gains also requires peering into the future. Artificial Intelligence (AI), as the gathering wave behind a renewed cycle of innovation, is gaining momentum among manufacturers worldwide. The major drivers of increased AI investments include larger and more complex datasets, or big data, access to infinite computational power in the cloud, and the evolution of a scaled, Industrial Internet-of-Things.
Despite – or perhaps because of – the pandemic, AI and machine learning investments in the manufacturing sector are not slowing: 57% CAGR is projected over the next five years. AI represents the cutting edge of technology’s ever-expanding frontiers – a springboard to further transform manufacturing, and feasibly the entire business model. But how manufacturers capitalise will require careful strategising and planning.
Smart systems, smarter factories, intelligent machines: Leaders should be thinking beyond the factory. Indeed, even now, innovative production is not happening on an assembly line or a hectic, noisy machine-cluttered factory. It’s occurring digitally – and the raw material is data.
If this sounds far-fetched, consider how the automotive industry is progressing the concept of self-drive cars; or how even whisky is being made by AI. Physical products themselves are increasingly connected and digitised, and manufacturers should be thinking about evolving from the process of producing products to creating value through digital innovation.
Capitalising through perseverance
Multiple analyses and studies confirm that digital technologies and related transformation initiatives drive revenue growth, refine operational efficiencies, leverage competitiveness, and deliver bottom-line margin improvements.
A meta-study comparing companies’ performance across two recessions and recovery periods between 2003-2017 concluded that the outperformers “made bold moves on growth” – measures which included exploring adjacent industries and expanding their value chains. And, post the 2007-2008 financial crisis, the study noted a correlation between better growth and digital capabilities in automation, multichannel, cloud and AI. These digital capabilities also correlated closely to the entities’ learning and collaboration scores. Overall, on average these outperforming companies achieved percentage growth rates three times higher than their industry competitors.
Digital transformation in manufacturing requires continuous, integrative improvement
Unlocking the significant benefits and full potential of digital transformation in manufacturing is best understood as a restless ambition. The forerunners of modern production systems, namely the Toyota Production System and other Lean models, strived for ongoing operational excellence and improvement; digitised systems should be viewed in the same context.
As such, continuous improvement practices and a Lean approach – ‘integrated,’ or ‘integrative’ in the context of digital operating systems – remain a foundation for iterative gains and the evolution towards higher levels of organisational capability. In Lean methodology, kaizen literally translates as ‘good change’, and as a philosophy it applies as powerfully within digital operating systems as in traditional production methods.
An important aspect of this is stabilisation and standardisation. Best practices require rigour and systemisation. Lock in the improvement gains by finetuning standards, and benchmarking for their associated, new KPIs.
The foundation already exists. Sustaining digital transformation initiatives will unlock further end-to-end value, and continuous and integrative improvement programmes are tools to embed and sustain them.
Seize the moment – with circumspection
Cycles of economic downturn do turn upwards. The Organisation for Economic Co-operation and Development (OECD) forecasts solid 4.5% global GDP growth for 2022. This is an encouraging indicator of recovery which will provide a more stable footing for digital transformation initiatives to be solidified.
The systems and supply chain shocks of the past 18 months are not yet behind us. But world-class organisations, those manufacturers with competitive ambition, have already been planning for the future. They understand that expanding digital capabilities is a prerequisite for innovation and growth.
The fittest will survive, and the very fittest will thrive.
Ready to take the next step on your digital journey? Download the TRACC brochure to find out how TRACC can help you unlock digital capability across your value chain.
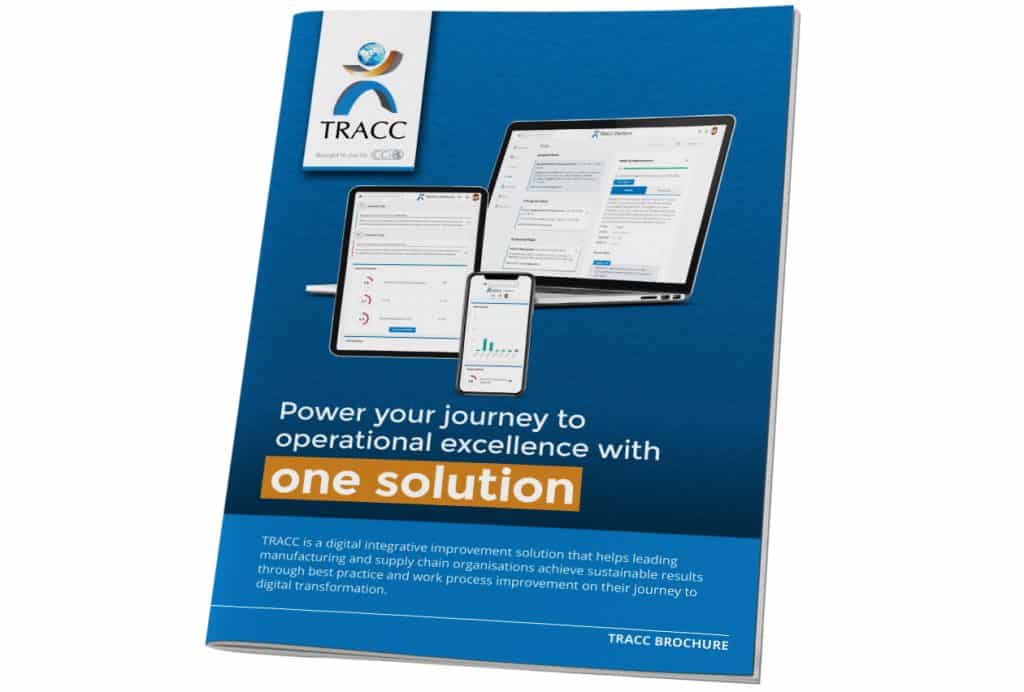