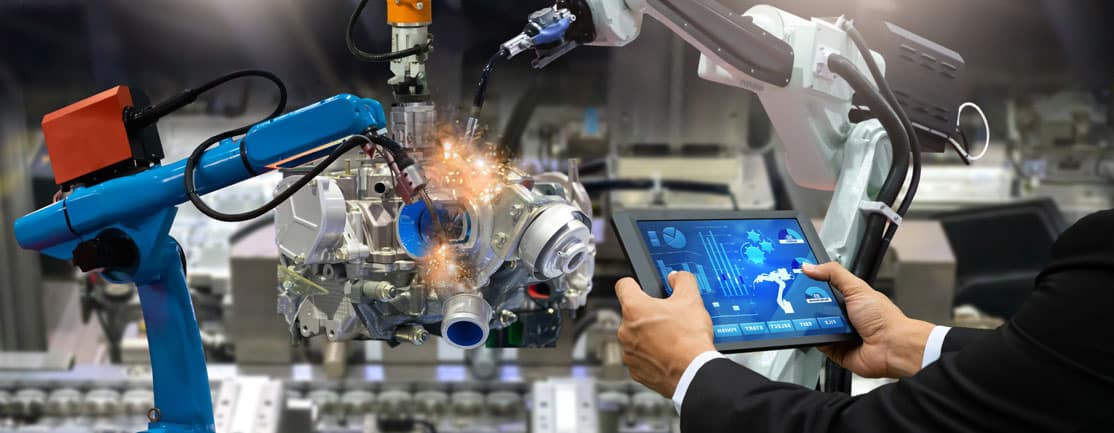
Balancing talent and technology: how leaders are driving 2030 manufacturing competitiveness
The metamorphosis of the manufacturing environment, powered by Industry 4.0 technologies and driven by its related disruption, must be strategically directed. Only companies that harness transformative capabilities will gain genuine competitive advantage.
Many manufacturers are currently strategising defensively or investing conservatively. Distinctive, progressive leadership is required to gear for next-level growth in the decade ahead.
Industry 4.0 is fundamentally changing manufacturing organisations’ structures, across the factory floor and throughout the supply chain. Leaders need to engage, urgently.
The effects, implications and opportunities of Industry 4.0 comprise the metamorphosis of manufacturing – a change that has already begun, and which is unravelling against the backdrop of global economic uncertainty and business volatility.
Digital technologies have opened new frontiers for automation, with the promise of exponential leaps as the footprint of artificial intelligence (AI) widens. (See the first article in this series, Reimagining the 2030 manufacturing workplace: way beyond automation, for a discussion of the realm of technology shifts.)
Hand in glove, these advances have sweeping impacts upon people – manufacturing’s workforce, managers of operations, and the talent pool for innovation. (Refer to the second article in this series, The road to the 2030 manufacturing workplace: what Industry 4.0 means for talent strategies.) The interlinked challenges of technology and talent require companies to invest wisely in both areas.
To do so requires envisioning the factory of the near-future, with Information Technology and Operational Technology (IT-OT) convergence, existing jobs performed by robots and, starting now, the emergence of entirely new job functions.
Above all, leadership now involves a heightened level of ambidextrous capabilities to operationalise these changes. To position the organisation for uncharted directions, leaders themselves must transform.
To fuse the power of technology and people, leadership starts with a vision
Envisaging change and how it will impact the organisation means challenging the basis of the business. The automotive industry may not have imagined the transport revolution even as recently as 20 years ago – but those companies that did would have seized competitive advantage in the development of electric cars, autonomous drive vehicles, and ideas on how to mitigate the sharing economy’s swing away from personal car ownership.
Unlock transformative potential by articulating the company’s mission. Business success now means a north-star purpose, beyond profits – and the stewardship of an enterprise now requires mapping its entire social footprint. This directly improves the bottom line: according to a Harvard and EY Beacon Institute study, companies prioritising purpose are significantly more likely to achieve 10% or greater revenue growth. 1
Leaders need to imagine their companies as digital-first entities. In all industries, the 21st Century will be one of radical uproot, primarily due to digitisation. Consider, for example, that even the food industry has already undergone immense change: the purchase cycle of packaged food has been influenced by online shopping. And the rapid spread of food trends via digital media has spawned broader consciousness of ingredients, as one manifestation of healthier choices by more informed consumers.
Communicate this vision. The thread from leadership to factory floor action is communication, to forge and nurture a crucial state of employee engagement. An engaged workforce adds multiple dimensions to any organisation; according to Gallup’s 2018 State of the Global Workplace report, however, just 15% of workers are actively engaged. In the US manufacturing sector alone, this disengagement is estimated to cost some $600 billion in lost productivity. Technology and culture change can – and should – be championed together to cultivate purpose-led work. (See side-bar ‘Culture-change adapts in the 4.0 paradigm’.)
Culture-change adapts in the 4.0 paradigm
The symbiosis between learning cultures and lean production is proven. But today’s complexities bring unique challenges, necessitating adoption of specific tactics in fostering a learning organisation:
- Boundaryless thinking. Connections and ideas can spring from surprising sources. In a commitment to learning, executives should be encouraged to deep-dive into wide-ranging business ambits. Information and expertise should be networked within and beyond the company.
- Nurture diversity – and diverse talents. A climate of participation and engagement requires stimulation and the ability to challenge and contribute.
- Accept the need to hurdle failure. The path to continuous improvement and growth permits – and may even require – the learning curve of failure.
- Strategise, incubate, test – then act. Technology costs are no longer prohibitive, allowing for quick action at comparatively lower risk.
- Budget for transformation. Because culture is often the biggest impediment to change, it requires concerted resource, including budget. Just as AI-IT-OT technology plans must be budgeted for, so too should programmes which upskill talent, migrate management to new capability levels, and energise the entire workforce to higher levels of engagement.
Transformative guide ropes for leaders: the road map to 2030 future-proofing
Within the factory, and throughout the supply chain, pushing the Industry 4.0 agenda is vital to the very existence of the organisation in the next decade. It’s vital that leadership heads the migration towards robotics, IT-OT convergence, and AI.
Set the appropriate pace of change. Lean manufacturers understand kaizen, the focus on continuous, incremental improvements. Stepping this up to kaikaku, a sweep of rapid and dramatic change within a production system, may be necessary to initiate transformation. But industry and company differences apply: Gartner, in their Hype Cycle for Manufacturing Operations Strategy, recommend adopting a smoothed approach if possible, to avoid hiccups in existing operating capabilities. Or consider a parallel transformation model: Toyota – famous as a forerunner of hyper-efficient, lean production systems – now has a Toyota Connected company within the group, specifically to drive machine-learning and serve as an experimental start-up in marrying data sciences and 4.0 technology with new forms of automated vehicles and mobility services.
Align the automation strategy with the business strategy. Understand the costs of automation in relation to labour, and how these are altering: average labour costs in US manufacturing, for example, are now more than double their 1990 prices; in the same timeframe, the cost of robotics has halved. In a recent study of automation’s global spread and its further potential within manufacturing, projections reflect that 64% of current human work hours were automatable using existing technology – the equivalent of saving, or substituting, a labour cost of $2.7 trillion. Although manufacturing is one of the most automated industries, the implication is that further replacement potential already exists, including within linked management, procurement and supply chain activities. 2
Ultimately, the degree of automation and its balance with the human workforce will hinge upon business needs and goals. Leaders need to actively assess these, and strategise appropriately.
Think innovatively, and intelligently, about innovation. Even disruptive innovation is rooted in operational excellence. In their book Great by Choice (HarperCollins, 2011), Jim Collins and Morten Hansen document the necessity of rigour, routine, and dedicated planning in forging scalable, sustained corporate success. Innovation is, fundamentally, earned, and based upon hard work. Or, as Thomas Jefferson wrote, “I’m a great believer in luck and I find the harder I work, the more I have of it.”
But maintaining a constant cycle of innovation and operational excellence requires a trade-off, especially involving investment allocations. Evidence supports the view that business leaders are weighing this conundrum too cautiously: in Deloitte’s State of AI in the Enterprise report of October 2018 the top identified benefits of AI were deemed as ‘Enhance current products’ (44% of respondents) and ‘Optimise internal operations’ (42%).3 Currently, investment remains biased towards improving existing systems, such as upgrading ERP software to refine data analytics, rather than being allocated to newer, more advanced applications such as robotics or integrated IT-OT sensor technologies. A mind shift is required to implement a less conservative technology strategy towards genuine 4.0 transformation. The potential for a quantum leap in productivity is largely being ignored.
Future-proofing leaders for 2030
Manufacturing companies require a new breed of leader, able to bridge the tension between vision and EBITDA delivery, to meet the expectations of internal and external stakeholders, and to navigate myriad demands inherent in a phase of enormous technological and societal upheaval.
Embrace VUCA. Volatility, uncertainty, complexity and ambiguity are now irrevocable aspects of business. Leadership, today, requires the ability to manage the innate problems of these new normal societal patterns, in a multifaceted and multi-skilled approach.
Understand risks. Paradoxically, deep-seated resilience is part of innovation. Planning for multiple scenarios generates a far-sightedness which blends reality and practicality with unconstrained thinking.
Embrace societal changes. An evolution is afoot in the psychology of the modern workforce, notwithstanding poor current levels of engagement. Motivating and managing a diverse talent pool may involve redesigning the architecture of teams to incorporate virtual collaboration, flexibility, and parallel teams. The nature of tomorrow’s workforce should be seen as an opportunity to unleash productivity, starting today.
It’s a fundamental principle of lean manufacturing that new capabilities are constantly sought. Today, leaders are required to shift what they do: from providing answers to asking questions; from seeking immediate fixes to identifying root cause; from setting purely broad corporate goals to guiding individuals’ work. Leaders may sense opportunity amongst these shakeups, but the ambiguity of global economic fundamentals, the volatility of short-term signals, and the uncertainty of societal shifts is currently reining in transformative actions.
Ironically, these are precisely the reasons to initiate bold steps. Ten years from now, the world’s pre-eminent manufacturers will be those whose leaders seized the day a decade prior.
1‘The Business Case for Purpose’, Harvard Business Review and EY, 2018, figure 3
2‘The great re-make: Manufacturing for modern times’, McKinsey & Company, June 2017, page 78
3‘Deloitte Insights Tech Trends 2019: Beyond the digital frontier’, Deloitte Development LLC, 2019, page 21