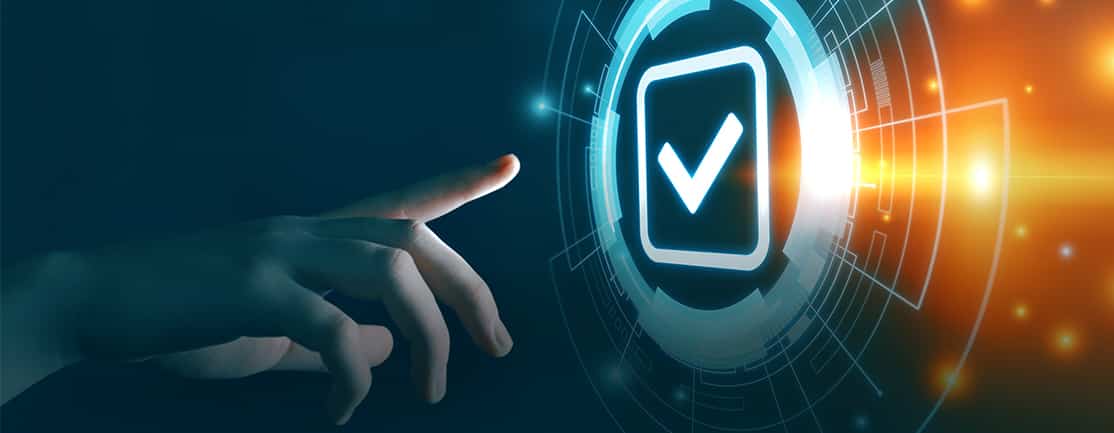
Developing organisational capability for the future world of work
Organisational capabilities are critical to business performance and include a unique combination of skills, processes, technologies and abilities that drive competitive advantage. These capabilities are key to organisational design decisions. Often, an organisation’s ability to meet its strategic objectives is constrained by its underlying organisational design – the challenge now is to identify and leverage the capabilities that will ensure success in the future world of work.
On 24 November 2020, over 215 delegates from 16 organisations ‒ including Diageo, Asian Paints, Cargill, Roche and Bayer ‒ attended Developing organisational capability for the future world of work, a free TRACC Community webinar hosted by Dr Dino Petrarolo, Senior Vice President, CCi, Asia-Pacific and featuring guest speaker Cecil Everson, Head of Manufacturing, Africa, Distell.
The primary focus of the webinar was organisational design in the digital age, and the speakers delved into the critical principles and practices that underpin successful organisational design, and enable organisations to transition to digital excellence.
Dino began the webinar by offering a definition of end-to-end value chains, emphasising the importance of focusing on all aspects of the organisation from procurement to end-user delivery in the quest for superior business performance. He also provided a definition of digital operations, explaining that it is essentially a digitally supported or fully digital organisational workflow.
Dino then went on to explain that a classic approach to improvement is an ‘inside-out’ one, where manufacturing becomes the core of the improvement initiative, resulting in a ripple effect across the broader supply chain. “In most organisations, manufacturing tends to be the drumbeat of the supply chain, so it’s a logical place to start,” said Dino. “This classic approach would be to ensure that you have consistency in manufacturing, followed by internal alignment in the supply chain, and external alignment across the value chain.”
This capability building approach has helped numerous companies achieve sustainable competitive advantage and significantly reduce costs. But for many organisations, the road to operational excellence is not without its challenges. Sometimes, improvement initiatives stagnate, and poor organisational design is often a contributing factor. Dino went on to explain that strategy is critical to organisational design success, as is a keen understanding of the principles that inform organisational design in a manufacturing context.
Some of these principles include:
- Delayering ‒ The flattening of organisational structures; three-tier structures (strategic, systemic, situational); evolving to a contemporary matrix.
- The creation of whole jobs ‒ No machine minders; operators are multiskilled across a process area; breaking down of silos.
- Standardisation, rationalisation and consolidation – Reduced number of roles and job titles, consistencies and pay equalities.
- Self-sufficient, accountable teams – SHERQ at source; autonomous maintenance; CI and problem-solving capabilities are developed.
- Menial manual jobs confined – Non-core, non-value-adding tasks and roles are reduced; technology solutions replace dependencies.
Organisational design and the supply chain
Dino then went on to look at organisational design and its application to the supply chain. “From a Theory of Constraints perspective, we know that your performance is as good as the weakest link in your chain, but in supply chain, it’s more strands of rope than a chain, so it’s much more complex,” said Dino. Strategy and principles are as fundamental in the context of supply chain as they are in the context of manufacturing.
Dino went on to expand further on the organisational design principles that can be applied to the supply chain:
- Teams are built around value chain processes (flow of work – products and services).
- Leadership approach and capability to create and support an environment where teams take accountability and are largely self-sufficient (i.e. empowering leadership).
- Competent teams that ensure quality of reliable and safe throughput where functional and support teams focus on systems, processes, standards and optimisation.
- Ongoing development of depth and breadth of skills applied to all teams to ensure continuity of effective team performance.
- Individuals have multi-team membership (i.e. individuals learn to have the maturity to work in and contribute to more than one team).
Organisational design and digital readiness
Research suggests that many organisations have moved from hierarchies/bureaucracies to market-orientated ecosystems. But organisations that are still steeped in traditional organisational design need to evolve in order to leverage the benefits of the digital age. The following diagram represents the three stages of organisational design maturity that organisations must move through to position themselves for a successful digital transformation.
Lean practice maturity is just as critical in the quest for digital readiness. “Your maturity will determine the success of your technology adoption,” said Dino. “If you want to take advantage of technology, you need to move your practice maturity to Stage 3 and be digitally ready.” The diagram below illustrates the five stages of practice maturity and how they prepare organisations for a successful digital transformation.
Dino concluded his segment by explaining that a rigorous change management process is critical when introducing a change to organisational design. “The change process can make or break the organisational design change,” he said.
The role of organisational design in Distell’s improvement journey
Guest speaker, Cecil Everson, explained how organisational design influenced global beverage leader Distell’s end-to-end supply chain improvement journey. He mentioned some of the challenges that the organisation faced in the bid to become future fit including: lagging customer service performance; supply chain structural challenges; a functionalised organisational design model and tacit knowledge possessed by few experts.
Cecil went on to discuss the model that Distell adopted to ensure that knowledge was easily accessible and shared across the organisation. “We used this model to determine how to move our tacit knowledge to enable us to make changes in our business much faster,” said Cecil. The redesign included the establishment of centres of excellence, enhanced teamwork and the development of principles and practices through a centre-led approach.
Some of the principles that guided Distell’s organisational design included:
- Standardisation towards best practice
- Visual end-to-end supply chain
- Accountability at source
- Effective and efficient decision-making
- Planning and supply chain stability
- Culture of relentless reflection and continuous improvement
- Customer service
- Grow leaders for tomorrow
Cecil offered a detailed insight into Distell’s new organisational structure which hinges on three key areas: Planning, Centres of Excellence and Support functions. He also emphasised the importance of cross-functional collaboration to drive end-to-end supply chain excellence.
To find out more about organisational design in the digital era, watch the webinar on demand.