CI tools increase yield for chemical production plant while retaining current cycle time and quality
Executive summary
A chemical production plant realised 8% in increased production yield of a key derivative and $40 000 in annual savings by applying CI tools and methodology.
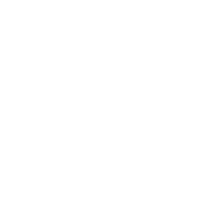
RESULTS
- Annual savings of $40 000
- 8% increase in throughput while maintaining current batch cycle time
- 8% increase in production yield of a key derivative
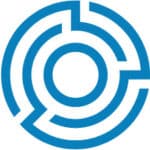
Challenge
- An old, inefficient making system was shut down and removed from service at a chemical manufacturer’s production plant
- The existing system, which was operating at 95% utilisation, required a capacity increase to retain the same yield level
- The challenge was to transfer the production throughput from the retired system to the existing system while maintaining current batch cycle times
- The formulation also had to be optimised without compromising quality, which meant the ratio of reacting to grinding would be critical
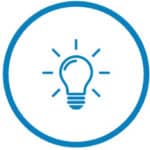
Solution
- Applying continuous improvement tools and methodology, the project team increased the batch size of the existing system by increasing the rate of raw material addition
- The team then reduced the overall mixing time, while increasing the milling rate and reducing the washing rate on the grinder
- In addition, the team was able to process more product through the grinder at the same rate, without any process upsets or adverse effects on product quality