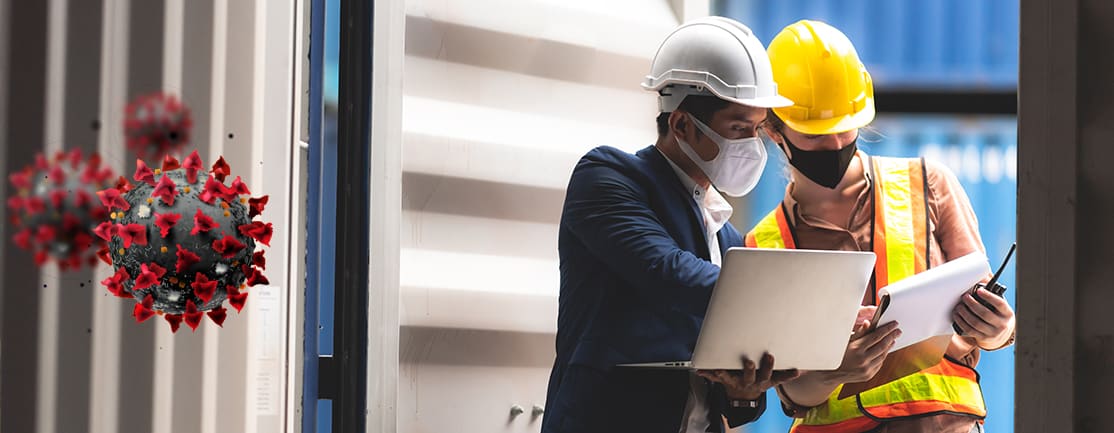
Impulsando la mejora y reduciendo costos: Medidas enfocadas para resurgir con más fuerza después de COVID-19
Es posible entusiasmarse con el recorte de gastos. Incluso frente a la crisis económica y cuando la recesión se avecina en la mayoría de los mercados del mundo, con líneas de fondo de empresas devastadas por factores extraños implícitos en la crisis por COVID-19, la administración de costos debería ser más que la de la crisis.
Antes de que se produjera la pandemia, muchas industrias ya se enfrentaban a enormes desafíos, como el cambio en las pautas de consumo y aumento del absentismo que afectaba al sector de las bebidas alcohólicas, o las repercusiones de las tendencias de transporte y movilidad de la economía solidaria para la industria automotriz. Las disciplinas de las mejores prácticas seguirán forjando la excelencia operacional, fortaleciendo los vínculos de la cadena de suministros de extremo a extremo y aumentando la resistencia de una organización. Pero las reglas han cambiado, y las empresas deben ver el paradigma actual no como un paréntesis antes de volver a la normalidad, sino como una coyuntura para rediseñar el ecosistema empresarial, mejorar las operaciones y acelerar los planes de transformación.
Esto requiere un enfoque estratégico de la gestión de los costos
Las empresas de talla mundial ven los costos como insumos para impulsar el crecimiento de los ingresos actuales y a corto plazo y las innovaciones para sostenerlos en el horizonte a mediano o largo plazo. El logro del retorno de la inversión (ROI) requiere del dinero invertido, del cual parte son gastos corrientes o abiertos a la empresa. Pero es la gestión de estos costos, su transparencia y cuestionamiento constante – lo que establece la diferencia de los elementos de la línea de costos y sus niveles en todo el espectro de la vigencia o despido. En resumen, la optimización de la reducción de costos se produce cuando se logra una mayor alineación entre la estrategia de la empresa y su ejecución.
Esto requiere una evaluación de los costos en toda la empresa, en todas las divisiones y en toda la cadena de valor. El objetivo es mejorar la eficacia de la empresa en todos los aspectos: operacionalmente, en términos de satisfacción de los clientes, compromiso de los empleados y devoluciones. El ajuste de los presupuestos para asignar los gastos donde pueda fortalecer las iniciativas clave, apoya el principio de un compromiso implacable con la mejora continua. Esto salvaguardará el rendimiento de la inversión de la empresa a corto plazo y la pondrá a prueba a largo plazo.
Priorizar y compensar la eficiencia frente a la efectividad
Para sincronizar la gestión de los costos con la mejora del negocio, categorizar los artículos potencialmente reasignables o extraíbles según lo que Bain & Company llama la curva de efectividad. Analizando tanto el grado de eficiencia (reducción de gastos) como de efectividad (mejora de los productos), las reducciones propuestas pueden agruparse en recortes de «ganancias claras», de «compensación» o de «último recurso».
La curva de efectividad
Fuente: ‘Digital lean: una guía para la excelencia en la manufactura’, Bain & Company, 2019
Considere la posibilidad de mantener las iniciativas a un costo menor colaborando con los socios del ecosistema empresarial que se enfrentan a dilemas similares. O bien, evalúe si la subcontratación de los proyectos seleccionados ahorrará costos e incluso, factiblemente, acelerará los plazos de cumplimiento
Ahora es el momento de investigar el verdadero estado de la empresa de lean
Los principios de Lean, por definición, tienen como objetivo inculcar la eficiencia organizativa en todas las funciones, con disciplinas continuas y técnicas de mejora. El sistema de producción de la empresa debe estar orientado al TPM para lograr un desempeño y una calidad de fabricación de primera clase, incluyendo el mantenimiento autónomo, la capacitación y las palancas e iniciativas de mejora enfocadas. Pero ¿cuán profundo es el principio en estos tiempos tumultuosos, en los que la cadena de valor se enfrenta a enormes desafíos tanto en el lado de la demanda como en el de la oferta, y en los que las limitaciones de costos deben equilibrarse con los planes de recuperación?
El comportamiento de la producción, la pérdida y los KPI de calidad deben ahora ser revisados y redefinidos estratégicamente, y el estatus de las 5S debe ser establecido y reforzado si es necesario. Además de mantener las iniciativas de mejora enfocadas como un pilar de la TPM, preste atención a otras dos áreas clave:
1. Objetivo de eliminación total de desechos
Los desechos de producción y la redundancia de los procesos deberían estar en el radar para protocolos más estrictos. Deben crearse y cumplirse políticas de ahorro de energía y agua. Los principios ecológicos no sólo ahorran dinero, sino que incorporan una cultura de prácticas sostenibles dentro de la empresa.
El alcance de los ahorros se ilustra en el Plan de Vida Sostenible de Unilever. Lanzado en 2010, en la década siguiente la empresa afirma que ha logrado una reducción acumulada de 1,000 millones de euros en los costos gracias a la mejora de la eficiencia energética y del agua en las fábricas, la reducción del uso de materiales y la disminución de los desperdicios. Tanto Unilever como el gigante de productos de consumo rivales Nestlé pretenden que todos sus envases sean reutilizables o reciclables para 2025; estos ambiciosos objetivos no tienen por qué coincidir necesariamente, pero el establecimiento de los objetivos de una organización para la agenda de la economía circular impulsará mejoras y ahorros de productividad.
El rango de otras mejoras factibles en este ámbito es vasto. Aunque es un requisito básico y rutinario del TPM, una auditoría de mantenimiento urgente puede ser considerada apropiada: la maquinaria y el equipo que no funciona óptimamente causa desperdicio y sobrecarga de costos. A un nivel más complejo, puede ser oportuna una auditoría de los costos de abastecimiento de materias primas. COVID-19 ha puesto de relieve los riesgos inherentes a las cadenas mundiales de suministros dispersas y justo a tiempo (JIT), y puede resultar revelador analizar los riesgos comparativos y la logística de una alternativa de nearshoring. El insumo de materia prima puede ser más costoso, pero el costo de abastecimiento holístico puede reducirse, y las relaciones de reputación con las comunidades locales y las bases de clientes pueden mejorar. Las compensaciones entre los costos unitarios de los materiales, las eficiencias de los sistemas y los ahorros logísticos deben ser cuestionadas como parte de la visibilidad de la cadena de suministro de extremo a extremo y de las comparaciones de costos
Lista de control de 10 puntos para alinear costos con la estrategia
- Adquirir una visión empresarial, no divisional o funcional.
- Base cero. Descartar el marco presupuestario del «último año más un porcentaje». Reevaluar costos en base a su necesidad de entregar la propuesta de valor de la empresa y permitir capacidades competitivas.
- ¿Se han evaluado todos los procesos y sistemas para obtener capacidades ágiles y flexibles? Estos atributos forjan la resistencia, y la velocidad de la toma de decisiones permite la mejora a lo largo de la cadena de valor.
- Racionalizar, cortar o subcontratar sistemas o proyectos de bajo rendimiento. La mejora continua requiere consistencia, y la mejora enfocada exige exactamente eso – enfoque.
- Comparar. ¿Se han orientado las áreas clave de rendimiento en función de los objetivos, haciendo referencia a los puntos de referencia internos, los promedios de la industria y los datos específicos de los principales competidores?
- ¿Se han reducido las capas de complejidad de los costos?
- Invertir en tecnologías que mejoren la visibilidad, la accesibilidad a los datos y las herramientas de apoyo a la toma de decisiones, como el análisis predictivo.
- Capacitar a los equipos multifuncionales para identificar e implementar medidas de mejora y proyectos de mejora de beneficios.
- Capacitar a los equipos multifuncionales para identificar e implementar medidas de mejora y proyectos de mejora de beneficios. Esto fomentará una conciencia permanente de los costos y una cultura de retroalimentación
- Mirar hacia adelante. Como respuesta a la crisis, ha sido necesario reducir los costos. Ahora, haga el ejercicio iterativo – una revisión regular de la eficiencia y la eficacia refuerza la disciplina de la mejora.
La eliminación del desperdicio y la redundancia también puede ser ayudada por las herramientas de análisis de datos. Es posible lograr mejoras significativas en el rendimiento y la productividad en el ámbito de la logística, por ejemplo, utilizando sistemas de almacenamiento que se sinteticen con los datos de la planificación de recursos empresariales (ERP) para racionalizar los procesos de almacenamiento, y aplicaciones de optimización del tráfico y de la localización por GPS que reduzcan las distancias de viaje, los tiempos de espera y los costos de combustible de las empresas de transporte por carretera. United Parcel Services (UPS), por ejemplo, afirma que ahorra hasta 400 millones de dólares al año gracias a la eficiencia basada en datos de las aplicaciones de Internet de las Cosas (IO) que optimizan la navegación a través de las 55,000 rutas de sus clientes sólo en los Estados Unidos.
2. El aprovechamiento de la tecnología es crucial para aprovechar las mejoras
En las plantas y en los pisos de las fábricas, la eficacia general del equipo (OEE) se mejora significativamente con las prácticas tradicionales de «lean», pero el nivel de mejora puede ser amplificado por las tecnologías digitales – hasta el doble, según algunos estudios.1
Como tal, resista la tendencia a dejar de lado los planes de inversión para una mayor automatización. El período de recuperación de tales inversiones será comparativamente rápido: el costo de las tecnologías robóticas se ha reducido a la mitad en los últimos 25 años, y la tendencia mundial es que los precios sigan bajando. Por el contrario, la curva de costos de la mano de obra está aumentando.
En una cadena de suministros más amplia y en los procesos SOP, las aplicaciones y herramientas basadas en datos deben aprovecharse al máximo. Por ejemplo, una comprensión más profunda de las estructuras de costos de los proveedores puede reorientar los procesos de adquisición para mejorar la posición competitiva y las decisiones de compra. Lo contrario se aplica: los análisis ricos en datos pueden arrojar luz sobre el panorama de los clientes, lo que puede ser inestimable para impulsar los márgenes mediante la formación de la demanda, la fijación de precios o la segmentación de los clientes.
Las iniciativas de transformación de las capacidades tecnológicas pueden entrañar complejidad. Racionalizar, integrar y simplificar siempre que sea posible: Gartner calcula un ahorro potencial de hasta el 30% en los gastos de software mediante herramientas de gestión de activos que optimizan la configuración de las aplicaciones y las licencias correspondientes.
Los líderes mundiales equilibran la resistencia a través de las crisis con la disposición a capitalizar más allá
El período inmensamente desafiante desencadenado por COVID-19 será una plataforma para que las empresas impulsadas profundicen la capacidad y la ventaja competitiva. Sus equipos directivos y de gestión darán prioridad a la reducción de costes como parte del proceso de mejora iterativo – viendo la oportunidad de negociar escenarios de ganancia mutua con los principales proveedores mediante la ampliación de los contratos a cambio de mejores descuentos; o analizando la cartera de I+D para racionalizar el número de proyectos a corto plazo pero impulsando la inversión detrás de los éxitos de taquilla respaldados para impulsar los ingresos en los próximos 5-10 años.
Más allá de la comprensible lucha por recortar el gasto discrecional, una visión más amplia es la de contextualizar los costos de la organización hacia el reenfocado y renovado desafío de la interrupción de 180 grados. Identificar esos buenos costos, los que impulsarán la mejora continua, sostendrán el retorno de la inversión y superarán de manera consistente la curva de costos de la industria. La evidencia de recesiones anteriores indica que las empresas que maniobran para evitar profundos recortes estructurales en los costos de la fuerza laboral y los sistemas, el capital de trabajo y las inversiones, superan a sus competidores después de la recesión.2
Las empresas líderes reducen los costos no porque tengan que hacerlo, sino con el objetivo de ser mejores.
1«Lean digital: una guía para la excelencia en la manufactura», Bain & Company, página 8, figura 4: la combinación de iniciativas digitales y lean puede reducir los costos hasta un 30% frente al 15% de los esfuerzos lean tradicionales
2En ‘Roaring Out of Recession’, Harvard Business Review, marzo de 2010, un estudio de 4,700 empresas en diferentes períodos de recesión y recuperación.