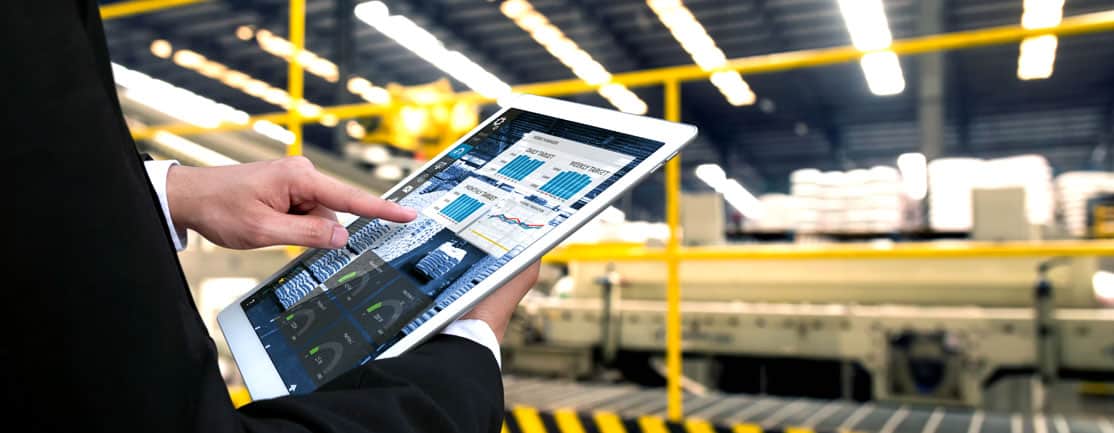
Transformación digital: madurez operativa es el plan de trabajo hacia la preparación
La era digital está a la vuelta de la esquina, anunciando un período de transformación y reinvención para los empresarios de todos los sectores. Desde robots más inteligentes y manufactura aditiva, hasta grandes datos y análisis prescriptivos avanzados, la Industria 4.0 trae consigo una ola de tecnologías que están cambiando la cara de la manufactura. Estas organizaciones están al borde de un cambio sin precedentes, entonces, ¿cómo se posicionarán frente al éxito? La clave es adoptar un enfoque basado en la madurez de la excelencia operativa para cruzar con éxito el umbral hacia un futuro digital.
A medida que más y más organizaciones entran en la carrera digital, la velocidad, agilidad y la adaptabilidad se han convertido en atributos altamente valorados. Y con buena razón: Las organizaciones que hacen el cambio a digital tienen una clara ventaja competitiva y están en una posición única para ofrecer la mejor experiencia al cliente. Pero existe el peligro de hacer cambios demasiado rápido: La preparación de su organización para Industria 4.0 requiere una evaluación y planificación cuidadosa, así como una visión profunda de la preparación de todas y cada una de sus áreas y procesos funcionales.
Según una encuesta de IDG (Estado de la transformación empresarial digital, 2018), “el 89% de las organizaciones tiene planes para adoptar una estrategia empresarial digital, sin embargo, solo el 44% ha adoptado completamente este enfoque”. Sin embargo, sólo las organizaciones con un nivel suficientemente alto de madurez en desempeño operacional obtendrán beneficios del cambio a digital.
El ciclo de Gartner Hype Cycle for Manufacturing Operations (Estrategia de operaciones de manufactura) de 2018 destaca específicamente este punto. Según el informe, “Las organizaciones que gestionan nuevas tecnologías y modelos de negocio requieren de asimilación a nuevas infraestructuras y procesos para una mayor madurez”.
Lo cual, según Gartner, ha revelado una debilidad en los sistemas establecidos TPS, TPM, WCM y aquellos basados en Lean, ya que no aprovechan eficazmente la tecnología con la coherencia necesaria. Por lo que el informe recomienda el uso de un “enfoque de madurez basado en etapas para definir el progreso iterativo y los logros por etapa para poner en fase el despliegue de su sistema de producción corporativo”.
Las cinco etapas de madurez en mejora del desempeño
Las organizaciones que han logrado alcanzar un desempeño innovador tienen una cosa en común: Han pasado sistemáticamente por cinco etapas de madurez estandarizada en mejores prácticas para construir las bases de una mejora sostenida del desempeño.
La siguiente ilustración muestra el viaje por las 5 etapas de madurez del desempeño:
- En la etapa 1, funciona en silos con poca sincronización entre la capacidad de suministro, demanda del mercado y la innovación de productos.
- En la etapa 2, las empresas construyen proyectos con expertos para resolver problemas (por ejemplo, calidad, exactitud predictiva de la demanda, lean). Sin embargo, una colección de proyectos individuales es de difícil gestión, y también es complejo construir capacidades de redes de valor del proceso final en esta etapa.
- En la etapa 3, las iniciativas de colaboración externa aumentan, y los KPIs y objetivos alineados se emplean en todas las cadenas de valor. La segmentación del cliente influye en los diseños de cadena de valor.
- En la etapa 4, existe un enfoque ágil y coordinado para crear valor óptimo. Se desarrollan estrategias detalladas para todas las cadenas de valor y las mejores prácticas se amplían a los socios. Esta etapa implica un cambio cultural enorme.
- En la etapa 5, la organización opera como una red de valor impulsada por la demanda de extremo a extremo (DDVN, por sus siglas en inglés) enfocada en ofrecer valor excepcional a los clientes. Los procesos están plenamente integrados, garantizando el desempeño del proceso de clase mundial.
El viaje de mejora del desempeño comienza con una evaluación de la organización, la cual determinará cuál es su puntuación de madurez global, así como las puntuaciones de madurez relacionadas con las personas, procesos y tecnología. En otras palabras, antes de comenzar el proceso de transformación hacia la Industria 4.0, las organizaciones deben definir su plan de transformación de acuerdo al nivel real de madurez de sus capacidades.
Determinar los niveles de madurez en toda la organización es vital, ya que permite a las organizaciones establecer una base de partida. Una evaluación de madurez debe revelar las brechas entre el estado de base y el estado final deseado; resaltar las áreas prioritarias; y proporcionar el mapa de ruta y el camino de implementación que guiará a la organización a la Etapa 5.
Crear fiabilidad y capacidad de respuesta en las operaciones de manufactura es el punto de partida crítico. Aquí es donde un sistema de mejora integral permite a las organizaciones diseñar y desarrollar procesos y crear capacidades y competencias en primer lugar, al mismo tiempo que se establecen las bases para una transición exitosa hacia un entorno digital.
Integración de la capacidad digital en toda su organización
Industria 4.0 aboga por el uso de tecnologías digitales para gestionar y monitorear cada aspecto de los procesos operativos a nivel de sitio. El Internet Industrial de las Cosas (IIoT), los sistemas ciberfísicos, la automatización, el análisis de big data y la computación en la nube permitirán la integración de silos funcionales y fomentarán una mayor conectividad de red. Los procesos de operaciones no solo serán más eficientes, sino que las nuevas posibilidades reforzarán la competitividad de su organización y reducirán los riesgos en las operaciones.
El camino hacia el desarrollo de las capacidades de Industria 4.0 será diferente en cada organización, y es probable que evolucione a medida que surjan nuevas tecnologías. A continuación se incluyen algunas de las capacidades fundamentales que su organización necesita desarrollar a lo largo de cada etapa del viaje de transformación digital, para asegurar el éxito a largo plazo.
- Capacidad de gestión de datos para obtener información precisa e utilizable necesaria para el análisis de datos importantes
- Sistemas estandarizados, como un sistema de Planificación de Recursos Empresariales (ERP), Sistema de Gestión de la Calidad (QMS), Sistema de Gestión de Mantenimiento Computarizado (CMMS) y Sistemas de Ejecución de Manufactura (MES), para apoyar la interconectividad
Identificación de los nuevos conjuntos de capacidades que operarios y directores necesitan desarrollar para utilizar nuevas tecnologías - Enfocarse en la implementación de los principios Lean para eliminar residuos y mejorar la agilidad
- Datos estandarizados de gran escala y análisis predictivo, informes de inteligencia empresarial y entornos virtuales
- Integración de sistemas dentro del sitio, como MES, QMS, Sistema de Gestión de Almacén (WMS, por sus siglas en inglés), Sistema de gestión de transportes (TMS) y ERP, con otros sitios clave
- Introducción selectiva de tecnologías móviles, inalámbricas, telemétricas, de computación en la nube y basadas en sensores para admitir la automatización y visibilidad
- Introducción de fabricación aditiva (impresión 3D) cuando corresponda
- Implementación de sistemas descentralizados autónomos y soporte de decisión artificial
- Máquinas conectadas y sistemas que permiten la supervisión remota, el diagnóstico, mantenimiento y la calibración dinámica, así como cambios automáticos y controles de calidad
- Integración de sistemas con los sistemas de los socios clave que permiten la reposición automatizada
- Uso de análisis prescriptivos avanzados, automatización y aprendizaje automático
Creación de fábricas autónomas
Cinco obstáculos a la transformación digital
Implementar Industria 4.0 vendrá con varios desafíos. A continuación se incluyen cinco áreas problemáticas que deben abordarse para asegurar un cambio digital exitoso.
Tendrá que desarrollar las habilidades y capacidades de sus empleados a medida que el enfoque se centra en la programación y el mantenimiento de las máquinas. Se requerirán habilidades avanzadas de TI, mecánica e ingeniería y deberán incluirse como plan de capacitación a largo plazo de la fuerza de trabajo. Un marco de mejora integral bien establecido será de gran ayuda para resolver este problema.
En estas primeras etapas de IIOT e Industria 4.0, existen pocos proveedores que pueden proporcionar soluciones clave. La mejor manera de compensar esta deficiencia es recurrir a tecnologías apropiadas de una serie de socios de automatización y tecnología de la información.
La transformación digital trae consigo un aumento de riesgos en seguridad. Proteja sus datos contra posibles virus y otros ciberataques con un monitoreo constante y una inversión en sistemas de seguridad.
Los estándares comunes aseguran la interoperabilidad de las tecnologías digitales entre organizaciones y son vitales para la conectividad global. Pero para desbloquear oportunidades de manera eficiente, la cadena de valor de su organización deberá adherirse a los estándares internacionales para conectarse e interactuar de manera organizada. Ya se han establecido varias asociaciones para definir tales estándares, como Industrial Internet Consortium y Smart Manufacturing Leadership Coalition en los Estados Unidos.
Las implementaciones de nuevas tecnologías siempre se encontrarán con cierto grado de resistencia. Es importante abordar inquietudes de los empleados que se resisten al cambio y mitigar sus preocupaciones sobre posibles pérdidas de empleos. Recuerde comunicar el cambio a todas las partes interesadas de la organización. Estimule el compartir perspectivas, preguntas e ideas.
Conclusión
En un mundo cada vez más digital, las organizaciones de manufactura necesitan ser más eficientes, flexibles y colaborativas para mantenerse al día con las demandas cambiantes. Los fabricantes que buscan optimizar sus operaciones necesitan comprender la interacción entre la mejora continua tradicional y la Industria 4.0. Se pueden generar sinergias valiosas implementando mejoras continuas y tecnologías de la Industria 4.0 de manera integral, en lugar de hacerlo de manera independiente o secuencial.
Al adoptar un enfoque gradual, basado en la madurez e integral para la excelencia operacional, las organizaciones serán capaces de adaptarse a las nuevas tecnologías emergentes al ritmo correcto, y asegurarse de que los sistemas, procesos y capacidades adecuadas están en curso para capitalizar las oportunidades de la era digital.